14 Best Practices for Lineman Safety, Part 1
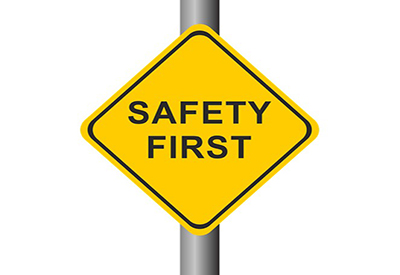
July 14, 2016
Appearing below is an excerpt of a paper presented by Wilson Yancey Jr. at the 2016 Academy of Electrical Contracting’s annual meeting in June: Cultivating Safety through Community: Training and Best Practices of the Electrical Transmission and Distribution Partnership. The academy was established by the National Electrical Contractors Association (NECA) in 1968 to recognize exceptional and outstanding service to the electrical contracting industry.
It was not so long ago that on-job injury and fatality information was held close to the vest by those of us in the electrical transmission and distribution industry. It was considered proprietary information, the kind of thing you didn’t want your competitors to know about your company.
In 2003, executive leadership from our industry decided it was time to take the unprecedented step of joining together to move aggressively toward reducing or eliminating injuries and fatalities.
The best practices that follow were developed by members of a U.S. industry group, the Electrical Transmission and Distribution (ET&D) Partnership. Over time they have become the standard in the industry. The complete best practices, including helpful FAQs, appear online at http://www.neca-neis.org/docs/default-source/powerline/best_practices_with_faq.pdf?sfvrsn=2.
1. Administrative controls
In order to address injuries due to improper job planning and risk assessment, this best practice requires pre-planning to begin at the pre-bid meeting and preliminary job site analysis to include the gathering of all relevant information needed to make a full risk assessment. This also suggests working on de-energized conductors and equipment whenever possible.
2. Pre-use inspection of rubber protective equipment
To avoid injuries due to worn, damaged or contaminated insulating equipment, all uniform components are to be inspected prior to use and removed from service if any defect is found.
3. Job briefings
Held at the project location at the beginning of each work shift, as work tasks or conditions change, and as additional personnel arrive on the job site, this best practice provides a standard methodology for sharing key information including hazards, protective equipment to be used, emergency response information and more.
4. Qualified observer
Injuries caused by unrecognized hazards and changes in work conditions can be offset or eliminated by the use of a qualified observer. These well-informed crew members ensure clearances are maintained, proper equipment is used, and effective cover-up is installed. This best practice also outlines the criteria of a qualified observer.
5. Insulate and isolate safety performance check
To ensure compliance with Isolate and Insulate procedures, this best practice requires a safety review process that includes assurances that company safety rules and proper cover-up procedures are being followed.
6. Cradle-to-cradle use of insulating rubber gloves and sleeves
Insulated gloves and sleeves are proven methods for reducing electrical contact injuries and fatalities. This best practice details the use of such PPE including when it is to be used and the requirements for the gloves and sleeves utilized while working from an aerial platform.
7. Lock-to-lock use of insulating rubber gloves and sleeves
As with the cradle-to-cradle use of insulated gloves and sleeves, the same equipment used while working on pad mounted equipment from prior to unlocking until relocking has been proven to reduce electrical contact injuries and fatalities.
*****
By communicating these best practices proactively and consistently, our industry will continue to see a trend of decreasing injuries as safety efforts that once were novel become the norm. Effective, trained, empowered leadership will deepen those efforts, which bringing us to our training programs.
Part 2, featuring the remaining 7 best practices, will appear in the August 16 issue of Electrical Industry News Week.
Wilson Yancey is the Vice President of Safety, Health and Environment for Quanta Services, Inc., and was made a fellow of the Academy of Electrical Contracting in 2015. Read the entire paper here: www.necanet.org/docs/default-source/academy-papers-(by-decade)/yancey—june-2016.pdf.