Stainless Steel: Understanding and Identifying the Ideal Enclosure Material, Part 1
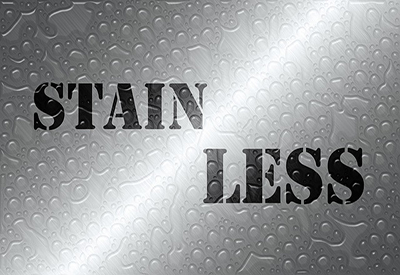
April 28 2016
Stainless steel is a steel alloy, consisting of at least 11% chromium. Chromium provides the shiny appearance stainless steel is known for, but also offers superior corrosion resistance. Unprotected carbon steel rusts quickly when exposed to air and moisture, degrading its mechanical properties and appearance. Stainless steel generally retains its properties in most conditions. However, there are some environments that can cause corrosion for stainless steel, such as low oxygen, high salinity (salt) and some extreme conditions (i.e., mines, strong acids). When stainless steel does experience corrosion, it is commonly by means of pitting, which appear as reddish spots on the surface.
The chromium present in the stainless alloy creates a thin, transparent passive oxide film when it comes in contact with oxygen. This film acts to protect the steel from corroding agents. While the film can be scratched away, the chromium present throughout the alloy allows the film to nearly self-heal instantly. If a zinc-plated, or painted, sample of mild steel is scratched, it will corrode and spread to areas beyond the scratch.
Stainless steel is available in many grades or formulations. The most common are in the 300 series, with 15-20% chromium. These are largely non-magnetic; however, forming and cold working can induce magnetic characteristics. The stainless steel in the 400 is typically magnetic due to higher levels of iron.
Stainless steel has become the standard material choice in many industries. For example, in the food and beverage industry, stainless steel allows for steam cleaning, while in pharmaceutical applications, stainless steel provides a clean, antibacterial surface. Stainless steel is also notable in various consumer products such as sinks and appliances.
Grades of stainless
There are many different grades of stainless steel to accommodate diverse application requirements.
- Type 304 is the most common grade of stainless steel, also known as 18/8 for its composition of 18% chromium and 8% nickel. The 300 series feature an austenitic crystal structure. Type 304 will resist corrosion in most environments; however, when exposed to salt and other chlorides, it will experience corrosion. In industrial environments, chlorides may be present in dust and flying ash, which if left unwashed on flat surfaces, will result in pitting.
- Type 316 is similar to type 304, with increased corrosion resistance due to more nickel and the introduction of molybdenum. Type 316 shows stronger resistance to a range of environments, and is recommended in coastal regions where salt is present in the air, especially within one mile of the coast. Salt can also be deposited via rain. Chlorides can also be found in cold weather environments where salt is applied to roadways. Salt road spray can be carried surprisingly long distances both vertically and laterally away from the actual road surface. Type 316 also shows increased resistance to corrosion by strong acids, which may be found in paper mills and mines. An alternative version to type 316 is type 316l, which has lower carbon content. Lower carbon allows for better welding characteristics.
- Type 321 is a grade typically reserved for weldments subjected to severe corrosive environments and high service temperatures from 800 to 1,600 degrees Fahrenheit. The formulation of type 321 is similar to type 304, with the addition of titanium. When type 304 is heated above 1,292 degrees Fahrenheit for an extended period of time it may suffer weld decay, which will initially display corrosion on the areas around the weld. Weld decay is lessened by the addition of titanium, making type 321 stainless steel ideal for use inside aircraft exhaust manifolds, boiler shells and fire walls.
- Ferritic alloys feature a different crystal that affords better corrosion resistance than austenitic grades. However, ferritic alloys are less durable than types 304 or 316 stainless steel grades. Ferritic alloys (types 405 or 409) are usually less expensive, and are most often used on automobile exhaust components.
- Martensitic alloys also feature a distinct crystal structure. They offer superior wear resistance but decreased corrosion resistance in comparison to austenitic alloys. Common martensitic alloy grades are types 410, 420 and 440, of which types 420 and 440 are commonly used in cutlery. Martensitic alloys are also highly machinable.
- Type 500 series alloys are heat-resisting chromium alloys.
- Type 600 series alloys are martensitic alloys, and are further strengthened through precipitation hardening, or age hardening.
- Type 2205 is a grade known as duplex, for its ferritic and austenitic characteristics. Type 2205 offers superior corrosion resistance with high strength.
In Part 2: a cost comparison between stainless and mild steel, available surface finishes, manufacturing processes, and a comparison to plastic and composite enclosures.
This article was first published as a white paper by Pentair. Read the entire document here: www.pentairprotect.com/wcsstore/AuroraStorefrontAssetStore/UserDownloads/WhitePapersCaseStudies/WP-00032_EN.pdf.