Stainless Steel: Understanding and Identifying the Ideal Enclosure Material, Part 2
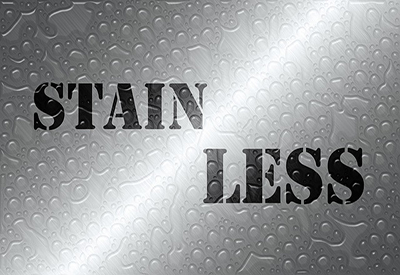
May 10 2016
Part 1 of this 2-part series looked at eight different grades of stainless steel, which has become the standard material choice in many industries. It is available in many grades or formulations to accommodate diverse application requirements. Here in Part 2: a cost comparison between stainless and mild steel, available surface finishes, manufacturing processes, and a comparison to plastic and composite enclosures.
Cost comparison
Stainless steel is significantly more expensive than mild steel; Type 304 is roughly four times more expensive than mild steel while Type 316 is roughly five times more expensive than mild steel. Additionally, the manufacturing process is more time consuming than mild steel, which increases production costs as well.
Surface finish
Stainless steel can be purchased in a variety of surface finishes, including:
• #1 — mill finish, a rough and dull finish
• #2D — annealed, pickled, dull cold rolled
• #2B — annealed, pickled, as rolled, cold rolled
• #3 — intermediate polished, applications include consumer products such as sinks
• #4 — standard polish, food and pharmaceutical grade
A stainless steel finish between a #3 and #4 finish has a protective masking applied to one side, which is left on the outside of an enclosure and will be removed as late in the manufacturing process as possible.
Surface finish does have an effect on corrosion resistance. Finer or more polished finishes have increased corrosion resistance, compared to coarser finishes such as 2B or mill finish.
Manufacturing
In general, manufacturing with stainless steel requires additional time and special care. Stainless steel products are usually left unpainted; therefore, special care needs to be taken to avoid scratches and blemishes. For example, to protect enclosures, a masking can be used on the outside surface to protect against scratches through the production process.
Stainless steel also has a grain direction that is visible on polished surfaces. Weldments should be laid out with the grain direction in the same orientation. The grain direction also affects corrosion resistance, as moisture moves parallel to the grain direction easier than across the grain. Enclosures should be designed to feature a vertical grain direction.
- Welding — the core welding process is essentially the same for stainless steel and mild steel. However, there are differences in the weld wire, gaps, additional blending and bluffing. The weld material needs to match the “host” material; thus, stainless requires additional consumables (types 304 and 316 wire for MiG welding). Other design considerations, such as weld gaps, should also be taken into account. Stainless steel is more challenging to weld and requires a higher level of craftsmanship to create an aesthetic look. These welds also require grinding, blending and buffing to give the weld an acceptable appearance; typically only grinding is required on mild steel welds. Since stainless steel enclosures are largely unpainted, these additional steps are required to hide weld imperfections. The welded joint is a common location to first notice corrosion. During welding, there may be iron particles present, which are embedded into the weld, especially if both mild steel and stainless are welded in the same facility. A process called passivation can be used to clean and re-establish the protective oxide film around the weld area. Passivation is generally done using an acid bath in which the material is dipped. There are also gels that can be applied locally to welds.
- Forming stainless steel uses the same process as mild steel. However, stainless steel can present additional forming challenges, as it tends to spring back more than mild steel.
- Painting — some stainless steel enclosures are painted, especially in outdoor environments where solar radiation is a concern. A painted stainless steel enclosure (light color) remains up to ten degrees cooler than an unpainted enclosure in direct sunlight. Paint also offers an additional level of protection against corrosion in extreme environments. Stainless steel can be painted using standard processes and equipment.
Comparison to plastics, composites
Plastics and composites are ideal alternatives to stainless steel in specific applications. Composites offer advantages over stainless steel, including providing a lighter design and easy modification options. However, Fiberglas composites can experience fibre bloom from UV rays, which is a common corrosion mode. A composite enclosure will likely have a lower cost than a stainless steel enclosure. However, in most situations, stainless steel offers better corrosion resistance and strength. Stainless steel is also better suited for extremely high or low operating temperatures.
Stainless steel is not recommended in environments that feature acids, such as hydrochloric and hydrofluoric, or in areas where ferrite chloride is present. In these applications, a polyester enclosure may be the better selection.
While a stainless enclosure is relatively quick to design, build and test, a composite enclosure takes additional time to design. The tooling for a composite design also requires significant time and more costs to develop. If the final composite enclosure is unacceptable or does not pass an aspect of testing, the formulation of the material can be changed, but modifying the tooling may not be possible.
Plastic and composite enclosures are quality insulators, while mild steel and stainless steel absorb and conduct heat better. If an application requires the enclosure to dissipate heat, a mild steel or stainless steel enclosure should be considered.
Summary
Stainless steel offers increased corrosion protection against environmental elements, while also providing a polished appearance and minimal maintenance. With a variety of grades and surface finishes, stainless steel can accommodate diverse application requirements while providing the necessary protection and performance. However, it is important to understand the enclosure environment before selecting stainless steel over other alternatives (painted or plated mild steel, plastics/composites), and also in choosing which grade of stainless steel should be used.
This article was first published as a white paper by Pentair. Read the entire document here: www.pentairprotect.com/wcsstore/AuroraStorefrontAssetStore/UserDownloads/WhitePapersCaseStudies/WP-00032_EN.pdf.