Choosing the Proper Components for Your Cable Assembly or Wire Harness, Part 1
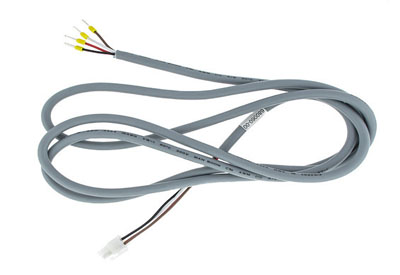
August 17, 2017
By Brian Morissette
A key component of any electronic or electrical system is the cable assembly/cable harness, yet it typically is one of the last components to be addressed. When designing a system the cable assembly should be addressed as early in the design stage as possible to allow for the best design to be specified for the application at hand.
Many components will be involved in the assembly design, and each component will have an impact on the performance of the finished cable assembly or wire harness. If an assembly that is either over-designed or under-designed is used, there will be negative consequences of the performance of the finished system.
Some of the up-front questions that need to be answered are associated with the environment the assembly will be used in. For instance, if the cable assembly is to be used in a dynamic installation, meaning it will be exposed to some degree of flexing, components of the assembly will need to be able to withstand the flex expected. The same choices would need to be considered if the assembly is to be used in a harsh environment, if the assembly is to be used in a clean room environment, or if the assembly is to be used where it would be exposed to sunlight or moisture.
In this two-part series, we will discuss the various options to consider when designing a cable assembly or wire harness, such as the best materials to use to meet the expectations of the assembly installation, the proper termination method for the type of signal that will be transmitted over the assembly, and what safety certifications the assembly will need to comply with based on the environment.
Conductors or circuits
The number and type of circuits or conductors that are included in an assembly will be determined by the application the assembly will be used in. Many options are available for the type of conductive material used, the stranding used to construct the conductor, and the plating applied to the conductive materials.
The most versatile and widely used conductor material is copper. Copper is compatible with numerous coatings to retard corrosion and to aid in the termination process. If more breaking strength of the conductor is a concern, options such as copper clad steel and copper alloys are available. These materials still employ copper but add either steel or alloys such as cadmium, chromium, and zirconium to increase both flex life and breaking strength. In some limited applications stainless steel can be used as a conductor, though stainless steel by itself is a poor conductive material when compared to copper and may have to be plated to improve its conductivity.
Bare copper is prone to corrosion from being exposed to the atmosphere, so most conductors are plated with various coatings to both retard corrosion and to allow copper to be used in more rigorous installations. One of the most popular coatings is tin, which is used to retard the corrosion of the bare copper, is the least expensive coating, and aids in the termination process. If the cable assembly is to be used in environments where higher temperatures will be seen, coatings such as silver or nickel can be applied and allow the conductor to be used reliably to temperatures of 200°C and 260°C, respectively.
The conductors used in an assembly can be constructed of just a single solid strand of conductive material or they can be constructed of many smaller conductors. Stranded conductors were developed as a means of overcoming the rigidity of solid wires and come in many variations, and the application of the assembly will determine which type of construction to use. For any given size conductor, the higher the number and the smaller the diameter of the strands, the more flexible the conductor.
Figure 1: Example of a stranded conductor (right) and a solid conductor (left). Both of the examples above are bare copper (no additional plating).
Each conductor of the cable assembly should be designed for the specific use it will be expected to see. For instance, if a conductor is to provide power, the amount of current it will carry needs to be considered before determining the size of the conductor to use. If a conductor will be expected to allow for the transmission of a signal, the speed of the signal and the length of the assembly need to be considered to determine the correct construction of the conductor.
Primary insulators/sheaths
Insulators are available in either thermoset or thermoplastic compositions, and as is true with the conductor construction, the material, thickness, and type used for the insulator of the primary conductors will be determined by the application that the cable assembly is to be used in. Materials are available to meet a broad range of applications and environments. Some of the critical areas to address are the operating temperature that the assembly will be exposed to, the type and level of voltage that the assembly will be expected to carry, the harshness of the environment in which assembly be installed, and the types of chemicals/fluids the assembly will be subjected to.
Materials are available that allow the operation of an assembly in temperature extremes of -65°C to +200°C or higher. A factor that needs to be addressed when thinking about temperatures is whether the assembly will be in a dynamic or a static state, meaning will the assembly be subject to movement, and if so at what temperature. An assembly that will be in a dynamic state at extreme temperatures will need more rugged compounds to enable it to function properly.
The amount of current or voltage that the cable assembly will be required to carry will also determine the type of insulation to be used. There are insulations that are not able to handle high currents for extended periods of time.
If higher speed signals are to the transmitted, some insulations will be “foamed” by using either a chemical foaming process or a gas injection foaming process. This foaming process will alter the insulation by creating air bubbles in the insulation allowing the passage of the high speed signal without being impeded.
The primary insulation can be coloured and marked for identification purposes in cables with more than one conductor. Colouring is completed by using a colorant that is mixed with the compound during the primary extrusion stage. An additional method of identification is by either printing a number on the insulation or by applying a stripe, which can be longitudinal, spiral, or in the form of ring-bands.
In Part 2: more options to consider when designing a cable assembly or wire harness, including conductor twisting/cabling, shielding, outer sheaths, connectors/strain reliefs, and safety certification.
Brian Morissette is Cable Assembly Product Manager Epec Engineered Technologies. This article was first published online by Epec: http://www.epectec.com/articles/choosing-the-components-for-your-cable-assembly.html