Room vs. Building-Based Control Systems: Pros and Cons
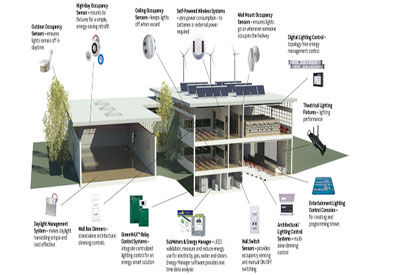
March 9, 2018
Steve Mesh
Room-based lighting control systems have been on the market for some time now. You might think of these as the younger cousins to larger building-wide or even enterprise-wide lighting control systems. However, that’s not an entirely appropriate comparison. For starters, what constitutes a “room-based” control system? That is an increasingly complicated question because the lines between system types are becoming more blurred as time goes on.
Typically, room-based controls have a central control module (“controller”). In lighting control system parlance, a “controller” is a device that contains a relay(s) to switch loads ON and OFF as well as output for sending dimming signals to fixtures. This is usually a 0-10V signal, although some controllers are designed to talk to DALI drivers and ballasts instead. Some controllers use other protocols, such as DMX. However, by far the most prevalent signal type used by architectural lighting control systems is 0-10V. One reason for this is that most LED fixtures have drivers that accept 0-10V wires for dimming control, and LED fixtures are becoming the light source of choice at an astonishingly accelerated rate. In fact, some states actually require that all LED fixtures are dimmable (i.e., California, which requires full-range dimming capability in the range of 10-100% for any LED fixture).
One vendor’s configuration for a popular room-based controller is a module that accommodates 20 amps of load. In other words, you can rout an entire 20-amp branch through this module. It contains 3 relays as well as 3 pairs of terminals for dimming signal output using 0-10V analog signals (one per relay). Therefore, effectively you can control fixtures in three “zones” (one relay and one pair of 0-10 output terminals per zone).
In many small spaces, this may be perfectly adequate. You could theoretically rout up to 20 amps (minus safety reserve) to any individual zone, but the more common usage would be to split the load between the three zones. For example, in a 30′ x 30′ classroom with three rows of fixtures parallel to the window wall, it would make sense for each row to be in its own zone. In fact, most energy codes require this anyway, since the row closest to the window wall is probably in the “primary daylight” zone and the next row is probably in the “secondary daylight” zone.
Most codes require fixtures in these zones to be controlled separately from each other, and from any other zones/fixtures in the space. Additionally, most codes now require that fixtures in these daylight zones automatically dim based on input from one or more photosensors. You can see how a control module that contains 3 relays and 3 pairs of terminals for 0-10V output can provide the code-required zoning in a small space. If the primary input to the fixtures is 277V, then one 20-amp control module will likely be adequate for relatively small, contained spaces.
In order to provide the functionality that is appropriate for most spaces, and to comply with code requirements, any lighting control “system” — even if it is limited in scope (i.e. a room-based system) — must allow for the use of sensors and switches. Many spaces must specifically use occupancy sensors to comply with automatic shutoff requirements. As previously indicated, many spaces also require that photosensors automatically dim fixtures in both the primary as well as secondary daylight zones. Most codes also require that local “area” switches are installed that allow for the “manual override” of the fixtures. In certain spaces, the owner might want more sophisticated local switches. For example, a “scene selector” switch with multiple buttons might recall specific light levels in a conference room or classroom (i.e. 100%/75%/50%/25%/full OFF).
Each vendor of room-based lighting controls makes most or all of these products for use with their system. Some make a variety of products in each category. For example, a given vendor may offer closed-loop as well as open-loop photosensors, or PIR vs. ultrasonic occupancy sensors (or even “dual-technology”). Obviously, if your project requires a specific type of occupancy sensor, photosensor or switch, it’s imperative that you confirm that a given vendor makes that type of product. Since sensors and switches use very little energy, room-based systems typically connect these peripheral devices to the centralized control module with Ethernet or other low-voltage cable. Therefore, this requires a separate run(s) from the wires that supply line-voltage power (plus low-voltage wires for the dimming signal) to the light fixtures.
What are the benefits of using a room-based lighting control system? For small spaces, the cost will be on the low side of the spectrum. If all you need is a system that can control up to 20 amps of load, split into three zones, then the control module as previously described should be more than adequate for the job. Another benefit to using a room-based lighting control system is that the wiring is relatively “normal.” What does “normal” mean in this context? It means that electricians are used to creating groups of fixtures in switch legs or entire branches based on line-voltage wiring. Keep in mind that if a control module has only 3 relays for output to turn fixtures on/off, then it’s only possible to distribute fixtures on the system among 3 zones (switch legs).
Historically, these room-based systems leave out certain functionality normally associated with larger building-wide or enterprise-wide control systems. For example, not all of these room-based systems have a scheduling feature. If the space in question contains occupancy sensors, then the “automatic shutoff” code requirement will probably be covered anyway. Typically, there is no easy way for these systems to take an ADR (automated demand response) signal and tell fixtures to dim accordingly during a period of peak load. That would require connectivity that these systems do not typically have. Similarly, recording or even just displaying energy use data may not be possible if the system has no method of connecting to other equipment or computer networks. However, by paring down the complexity of the equipment and associated software, vendors have created room-based systems that may seem much more straightforward to wire and commission to most electricians – and will likely be the lower-cost option for installing lighting controls in a given space.
What are some potential drawbacks to using a room-based control system? If the amount of load in the space exceeds the limitation of a given control module, then additional control modules would have to be used. Similarly, what happens if you require more zones of control than the system allows (i.e., more than the 3 that is used by the module previously described)? If the module has 3 relays, then there is no way to split the fixtures into 4 or more zones. What would happen if, at some future date, the space needs to be reconfigured and existing zones of fixtures need to be split? If you are already using the maximum number of zones based on that control module, then you would be forced to buy a new control module to get additional zones of control.
The native software in a given room-based control system may lack certain functionality, as previously mentioned. If you don’t need any of the functions that were left out of the software, go for it. However, if you commit to using a building- or enterprise-wide type of lighting control system, the likelihood is that you’ll have all the functionality you could possibly need. This may very well include functions such as scheduling, energy reporting, and demand response. Keep in mind that some of these may be required by code. So if you plan to use a room-based system, you really have to make sure that a system you purchase and install will meet the needs of the space as well as any current code requirements.
It should also be noted that some room-based lighting control systems use “remote controllers” (such as infrared remotes similar to those used for TV) to commission, program or reprogram the system. What happens if you lose the remote? Or don’t know how to use it in the first place? Will you have to pay the vendor to come and program the system for you? If so, this may reduce the financial advantage of using a seemingly “simpler” system. The trend these days is for control system vendors to allow for commissioning, programming and reprogramming via more ubiquitous devices, i.e. cell phones, tablets, laptops, etc.
Many (if not all) larger building-wide lighting control systems allow for the use of fixture-integrated controllers. As such, every single fixture can essentially be in its own zone. If this is paired with the use of fixture-integrated sensors, then any desired zoning can be achieved – now or in the future. Zoning (as well as rezoning at any future date) is a simple matter of pulling specific fixtures into any given zone in the software. Most systems that make use of fixture-integrated sensors have features in the software that allow for “grouping.” For example, in a conference room, the occupancy sensors in all fixtures may be in a single “motion group,” so that if just one of the sensors picks up a person entering the room, all fixtures will go on.
These trends among lighting control system vendors are very strong, particularly the use of fixture-integrated controllers and sensors, as well as much more simplified software that most neophytes can program with their cell phone. Since these systems typically come packed with full functionality in terms of what you can do with them, you clearly can’t go wrong if you opt for using building- or enterprise-wide lighting control equipment. If the financials pencil out, then how would you justify using a more limited system with restrictive zoning instead of a more fully-featured system?
Lastly, as previously stated, the lines that separate room-based lighting control systems from their larger building- or enterprise-wide cousins are becoming very blurred. For example, one vendor of a very popular room-based system resisted the development of fixture-integrated controllers as well as the development of wireless products. After evaluating trends in the market, they decided to augment their product line and now offer individual fixture controllers as well as wireless products. One issue that may have affected their decision to create individual fixture controllers is that this is a requirement in order to get onto the DLC Qualified Products List. As of now, this system is in fact on the DLC’s QPL.
Other products that augment the base equipment for a room-based system also help to blur the lines. For example, some systems now allow you to connect separate room-based control modules via routers, gateways, network bridges, etc. If these are ultimately connected to a centralized server, then you may end up with something that is more or less a building- or enterprise-wide lighting control system. Just make sure to check that this won’t require an inordinately complex array of components to turn a system that was conceived for use in an individual space into one that can handle the needs of an entire floor, building or campus.
Published with the permission of Lighting Control Association.
Steven Mesh is an award-winning lighting designer who has designed lighting and control systems for a variety of project types (commercial, museums, schools, residential, restaurants, retail, historic, healthcare, etc.). As an educator, he has taught classes and given presentations about lighting and controls across North America and internationally. One of his is developing lighting and lighting controls courses that rely on hands-on and/or interactive content. He has been a repeat speaker at LightFair for many years.