Why Do Some Workers Take Risks?
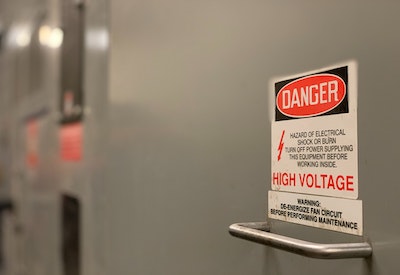
May 13, 2020
Many of us take risks in their daily lives, such as using our cell phone while driving or exceeding the speed limits, while fortunately avoiding any potential injury and damage. We are rewarded by a certain convenience when we take risks, such as apparent time savings as well as the tacit approval of observers who do not oppose our risky behaviour.
To reduce injuries in the workplace, we must all recognize that we are accepting certain risks on a daily basis and acknowledge the factors influencing risk tolerance.
10 factors influencing risk tolerance
1. Overestimating capacities or experience
“It will never happen to me.” People tend to take more risks when they rely on their physical capabilities, their strength, their agility, their reaction time and their reflexes to prevent an accident. A worker may overestimate his physical capabilities and tolerate a greater risk for tasks requiring physical strength. Or he could overestimate his agility and accept to work on a poorly adapted surface. This factor is also related to situations or to an experienced worker who uses his years of experience and his knowledge to justify taking risks at work.
Strategies to reduce tolerance: Give careful thought about your role as a mentor. Admit that despite your experience, there are always risks. Acknowledge your abilities, but continue to apply all policies and procedures correctly.
2. Familiarity with the task
“I did it 100 times before without any incident.” It happens when a worker performs a task several times successfully while having the capacity to do it without thinking about it. It’s a state called “unconscious competence.” Research shows that workers in that state might not be made aware of potential risks. This autopilot mode happens when a worker does not need to focus, preventing him from detecting potential hazards.
Strategies to reduce tolerance: Bring back your awareness to the task at hand. Perform each task as if it were the first time, or think about how you would teach this task to a new worker.
3. Potential severity
“It can’t be that serious.” In this case, the risk is known. However, the worker underestimates the seriousness of the potential consequences. The worker may think that the worst that can happen is a simple scratch, when in reality consequences can be much worse.
Strategies to reduce tolerance: Stop and think: “What is the worst that can happen?” Think about the potential and actual consequences, and not only the most probable. Do not minimize the risks!
4. Voluntary actions and sense of control
We more easily accept the risk of an action when undertaken voluntarily. Once we have decided to participate to an activity, whether at work or outdoors, a process called “confirmation bias” kicks in and we convince ourselves that it is safe despite the actual risks. This confirmation bias is amplified when we are in control or we believe to be in control over a situation. Control gives a sense of confidence in our capacities leading to underestimating the risks.
Strategies to reduce tolerance: Integrate the “Stop and think” method into all your activities.
Before and during a task:
Stop and think
• What could go wrong?
• How serious could it be?
• Do I properly understand the task?
• Has anything changed?
• Am I physically and mentally ready?
• Do I have the right tools and equipment?
Act
• Make this task safer.
• Use the right procedure.
• Use the proper tools.
• Reduce the risks.
Stop if you can’t perform the task safely!
5. Personal experience
Personally experienced events can haunt a person for a long time, even throughout their entire life. They can have an impact on his decision process regarding the performance of tasks associated with a negative event. It can decrease his tolerance related to a similar task. However, a worker who has never experienced a serious consequence from a task will accept a higher risk level., doubting the possibility that something dire may actually happen to them. New employees must listen to the testimonies from past victims of severe accidents in order to reduce their unconscious level of risk acceptation.
Strategies to reduce tolerance: Supervisors, observers, mentors and other “guardians of the corporate memory” have the obligation to ensure that workers are aware of past incidents caused by a lack of adherence to safety procedures and show the gravity of the consequences.
6. Cost for non-compliance
The personal cost may change the decision to accept a risk and can be influenced by how high the non-compliance cost will be. If the non-compliance cost (taking a risk) is great, such as losing a job or being fined or receiving a penalty, the person may decide to act in a less risky way.
Strategies to reduce tolerance: Identify and increase the non-conformity cost while removing barriers and increasing the reward for compliance.
7. Confidence in the equipment
Overconfidence bias happens when a worker overly trusts equipment, certain the tool will always work as intended. When a worker becomes familiar with specific tools and equipment, and has never experienced defects, he can become overconfident that it will never malfunction. This can happen on simple equipment, such as hand tools, or even more complex systems such as computer controls.
Strategies to reduce tolerance: Add equipment and engineering limitations to your training. Stop and think: “What would happen in case of an outage or a malfunction?”
8. Confidence in the protective and rescue equipment
Risks become more frequent when the limitations of the personal protective equipment (PPE) are not understood. Higher risk levels are accepted when workers place all their trust in the safety equipment they use and believe that if something goes wrong, they can rely on that personal protective equipment to protect them. For example, a shock-resistant glove cannot prevent the amputation of a finger.
Strategies to reduce tolerance: Understand the limitations of the personal protective equipment (PPE) and rescue devices. Consider them as your “last line of defence.”
9. Potential benefit and action gains
This risk tolerance factor stems from the desire for profit, gain or recognition. It happens at an individual level where the person may seek to take advantage of his own action; for example, finishing a task earlier by neglecting some steps. It can also occur at an organizational level when a company tries to reduce costs by neglecting certain safety measures. The gain could be direct, such as financial gain, or indirect, such as increased recognition. People can dangerously increase their risk tolerance when rewards are perceived as more important than the risk itself.
Strategies to reduce tolerance: Remove all rewards for taking risks and eliminate any restriction from adopting safety behaviours.
10. Mentors accepting risks
The level of risk tolerated by mentors has a direct impact on the level of risk accepted by individuals. Workers will observe their peers, supervisors and mentors to determine the procedures to be followed. It is important to define mentors in a work group and measure their risk tolerance.
Strategies to reduce tolerance: Identify the risk takers (including you) and rectify the situation. Admit where and when standards are not properly applied and correct the situation immediately.
Risk perception deals with the ability of workers to understand how a hazard can cause an incident or damage. The most important question that remains is risk tolerance. Generally, we (individuals, work groups, company departments) can accept a risk that is too high. The necessary process to help workers takes the proper decisions generally involves determining the acceptable level of risk according to the training on hazard recognition received. The solutions to risk tolerance can be found in the processes that help raise awareness of individuals and better identify the risks to help understand the risks. This way, they will be better equipped to make informed decisions concerning potential risks.
This article was first published online by SPI Health and Safety; https://www.spi-s.com/en/blog/ohs-leadership/why-do-some-workers-take-risks. The company’s mission is to be the single most valuable partner for companies that value health and safety in their work environment.
Photo by Troy Bridges on Unsplash