Arc Flash Incident Involving a Maintenance Switch
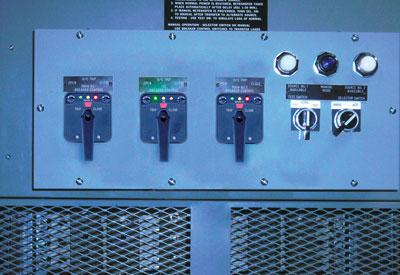
Feb 12, 2016
This case study article examines the plans and processes reviewed and considered, the strategy deployed to manage/reduce arc flash hazards, and then lessons learned in the implementation of new systems to improve electrical workplace safety. The setting: a chemical processing facility with a robust electrical workplace safety process. The site experienced an actual arc flash event while energized work was being performed.
Photo courtesy: www.utilityproducts.com
The facility was planning energized work for an existing 480 V low voltage switchgear assembly that was an existing piece of equipment in the plant. During a process upgrade in the facility, an energized work permit was issued to remove three abandoned load conductors from an existing 480 V low voltage switchgear assembly cable compartment.
The work permit was very detailed and included tools planned for use in the project and required PPE for workers performing the task based on the incident energy defined by a recently completed arc flash hazard assessment. The defined task for the work order required the site contractor to use a nylon rope, which was typical with this type of project, disconnecting the de-energized cables and working to raise them from the top cable compartment. Figure 10 showsa layout of the low voltage assembly involved in the work.
The de-energized cables were to be removed from Cubicle 5, with still energized conductors existing in Cubical 4 at the bottom of the cable wireway. The rope used was not able to grab the conductors and would slip off of the cable, so the electrical contractor elected to employ a “come along” to assist in the removal, as the come along could apply more force. The first conductor was successfully removed with this new tool. Upon removing the second conductor, a small arc flash was observed in the lower compartment. Simultaneously, the lights to the plant went out.The contractor stopped work and waited for plant electricians to arrive, not knowing what had just occurred.
The event caused the entire plant to shut down, stopping work on the project until an analysis could be completed. It was determined that the chain of the come along had drifted below where the work was being performed and into energized Cubicle 4. Fortunately, the damage to the wall of the switchgear and come along tool was minimal, which is shown in Figure 11.
Post event analysis proved that the chain of the come along had drifted below where the work was being performed and into an energized cubicle. The chain touched an energized terminal and arced to ground, touching both phase conductor and cabinet ground metal below the non-energized cubicle where the electrician was working. After reviewing minimal damage and completing the project while de-energized, the plant switchgear was cleaned and re-energized. Fortunately, total downtime for the plant due to this event was minimal. No loss of equipment or injury to any employee occurred as a result of this event.
Low voltage assembly involved in planned energized work. The planned task included removing cables from de-energized Cubicle 5 while Cubical 4 in an adjacent section was still energized.
The important take-away here is that the arc flash study was completed before energized work was performed. The upstreamlow voltage power circuit breaker with a special maintenance switch setting discussed previously employed technology to clear the fault faster than the microprocessor instantaneous setting of the circuit breaker trip unit.
Calculations were previously performed that quantified a reduction in incident energy from 17.7 cal/cm2 to2.9 cal/cm2 using the special maintenance setting. Both workersand equipment were saved as a result of a total clearing time at 40 milliseconds as defined by the manufacturer’s published trip curves[8].
Lessons learned
This case study unequivocally proves that planning for the unplanned event can save lives. Some of the key lessons learned here:
• mistakes will happen on even the best planned projects. A change in tools is what led to this arc flash event
• proper planning and leveraging of all accessible resources prevented what could have been a catastrophic event
• leveraging technology can often deliver a reduction in the available energy. Using more sensitive settings can save both people and equipment should an arc flash event occur
At left, a “come along” tool used for energized work and at right, damage to panel after phase to ground arc flash event with an upstream device with maintenance setting capabilities.
This case study is one of four published online by Eaton and has been lightly edited by EIN. See all case studies: http://www.eaton.com/ecm/groups/public/@pub/@eaton/@corp/documents/content/pct_1562591.pdf.