Alert: Electrical Lockout Using Manual Motor Controllers
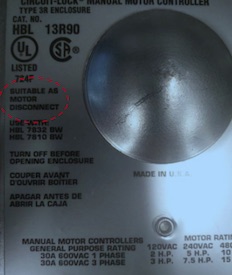
June 28, 2018
Workers in industrial workplaces such as office buildings, factories, arenas, shops or offices who are required to work on manual motor controllers (MMCs) or other electrical equipment may be at risk of serious injury or death if the electrical equipment is not stopped, de-energized and locked out and tagged before work starts.
Manual motor controllers are typically used to control motor driven equipment such as commercial heating, ventilation and air conditioning units. They also serve as a motor starter/controller, and sometimes as a motor disconnect.
Typically, MMCs should be marked with the words “suitable as a motor disconnect” (shown in photo). If they are not marked “suitable as a motor disconnect”, they should only be used as a motor starter/controller.
Using an MMC without the marking “suitable as a motor disconnect” as a lockout point is a hazard because the device contacts could weld together and provide a false sense of locking out. This could lead to electrical current passing through the contacts even with the device switch in the OFF position. Without testing to make sure there is zero energy, a worker would not be able to detect whether or not the contacts have welded together.
Here are possible contributing factors to contacts becoming welded together:
• contamination or corrosion of the contact surface, which can increase contact resistance, raising the temperature at the points of contact
• a loose rivet joint, a poor weld, or brazed joint, which can result in contact heating
• poor contact alignment, which reduces the effective contact area
• currents that are higher than normal
Care must be taken when installing the switch with the MMC so that it is oriented to correspond with the on/off marking on the switch. If the switch is installed backwards the power could be on when the switch enclosure indicates that it is off.
What you’re required to do by law
1. Lock and tag the power supply. Under provincial health and safety requirements, the power supply must be disconnected, locked out and tagged on or near live exposed parts of the installations, equipment or conductor:
• before any work is done
• while work is being done
2. Check to ensure lockout requirements are in place. To ensure suitable lockout requirements are in place, review and compare provincial requirements to your company policy and procedures. Update your policy and procedures if needed.
3. Ensure workers understand and implement the policy and procedures.
Recommended precautions
To help prevent injury or death from electrical contact, follow these precautions:
• employers must make sure that effective precautions are in place to protect workers (e.g.,, ensure that each controller is used appropriately)
• include in your work practices how to respond to unexpected events, such as equipment failure; in this instance, the welding of contacts within a MMC
• make sure that contacts are suitable in size and material for the installation
• ensure support members for electrical contacts are as highly conductive as possible to help keep the contacts cool
• always confirm the absence of energy by correctly testing, with an approved device rated for the purpose, prior to making contact with any exposed parts
• consider all electrical equipment and installations as energized until they are proven otherwise
• do not use an MMC as a disconnect unless it is marked as “suitable as a disconnect.” For example, Rule 28-602 (3) (1) (b) of the Ontario Electrical Safety Code indicates that MMCs marked as “suitable as a motor disconnect” are acceptable to be used as both a starter and a means of disconnecting
This article was adapted from an alert published by Ontario’s Ministry of Labour. Read the alert here: https://www.ontario.ca/page/alert-electrical-lockout-using-manual-motor-controllers?_ga=2.207404499.1594584926.1519129932-250485158.1518102964
Photo source: Electrical Safety Authority