A Revolution in Arc Quenching Technology
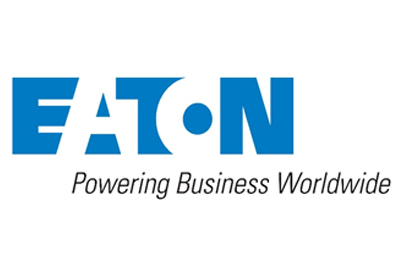
Sponsored by Eaton
June 7, 2018
The danger associated with arc flash is well known to those working in the electrical industry, however knowledge of the potential danger does not remove it, although it certainly does help limit the potential for an incident.
While awareness, engineering and administrative controls have increased, it is still estimated that there are between 5 and 10 arc flash incidents a day in North America. Arc flash events occur when insulation or isolation distance between energized conductors is compromised, allowing the current to travel through the air between the conductors. Major causes of arc flash events include tools left inside equipment after maintenance, loose electrical connections, animals entering the equipment to stay warm or ingression of water or other conductive material. To reduce the risk of arc flash, there are many standards in North America that identify incident energy reduction methods for example, CSA Z462 – 2018 and NFPA 70E – 2018.
There are also several legal statutes in place to protect workers operating in hazardous locations such as those presented by electrical work. For example, the Occupational Health & Safety Act of Ontario (OSHA) outlines that employers must “take every precaution reasonable in the circumstances for the protection of workers,” and can fine corporations up to $600,000 per offense, and individuals up to $27,500 or 1 year in jail.” This mandate does not refer specifically to arc flash incidents, but they certainly fall under this blanket.
Other provinces have directly addressed arc flash concerns. Alberta’s Occupational Health and Safety Code requires that workers that are exposed to electrical equipment flash-over wear flame-resistant outerwear and other Personal protective Equipment (PPE) appropriate to such hazards.
Federally there is no specific regulation regarding arc flash concerns, but in 2004 Bill C-45 was implemented that does establish a duty under the criminal code of Canada for employers, managers and supervisors to ensure a safe and healthy workplace. Under this Bill there is no specific fine limit but individuals found guilty of negligence causing death can face life in prison.
Having noted these regulations, those working with electricity are beyond question working in a dangerous profession where minor mistakes or faulty equipment pose serious concerns. However, utilizing proper PPE, following workplace safety procedures, and training aids can minimize arc flash incidents. Ensuring staff have the proper training, like the Eaton’s Arc Flash Hazard Training or online Arc Flash Prevention Launch Tool, that provide details on arc flash safety and available arc flash safety checklists, is a simple step that can be taken to protect both employees and the company.
However, in this article we are going beyond training and awareness to look specifically at the technical advances that have been made to protect workers in the event of arc flash, and in particular a new product developed by Eaton that has taken arc flash safety to the next level.
Eaton and the industry in general are increasing their attention toward arc energy reduction as critical means for arc flash safety. Of the various arc energy reduction methods, the most promising is Energy-Reducing Active Arc Flash Mitigation Systems. However, to fully understanding this revolutionary approach we need to briefly consider the traditional methods of arc-energy reduction.
Arc energy reduction methods broadly fall into several categories, including zone selective interlocking, bus differential relays and arc detection relays. The primary issue with these methods is that they rely on tripping an upstream circuit breaker to clear the fault. However, the time required for a circuit breaker to clear the fault may not be fast enough to adequately reduce the risk posed by the arc flash.
For example, Eaton has identified that an arc flash pressure wave in low-voltage metal enclosed switchgear peaks around 7 milliseconds. However, low-voltage switchgear employing the above-mentioned arc energy reduction methods can take up to 4 cycles or 67 milliseconds to clear the fault. For a system to be most affective, the total operation time of arc energy reduction should be less than 7 milliseconds. At present, devices capable of reducing arc energy within this timeframe are classified as Energy-Reducing Active Arc Flash Mitigation Systems.
Previously, Energy-Reducing Active Arc Flash Mitigation Systems have been limited by the clearing time of the upstream overcurrent protective device. However, arc quenching, which employs an alternate means of energy reduction is also classified as an energy reducing active arc flash mitigation system.
Arc quenching works in unison with an arc flash relay to detect the ignition of an arcing fault. Once detected, the arc flash relay sends two signals, one to trip the main or upstream circuit breaker and another to the arc quenching device. Once the quenching device has received the signal the arcing fault commutates to the quenching device where it is safely contained. This commutation, or quenching, can occur in less than one cycle, much faster than the clearing time of a power circuit breaker. This results in less incident energy and reduced arc flash damage to the switchgear.
There are two primary forms of arc quenching devices. The first is a device that creates a very low impedance current path by applying a three-phase bolted fault to equipment which collapses the system voltage, extinguishing the arc, which then requires the upstream breaker to clear the bolted fault. This method draws maximum peak fault current when triggered, which can result in damage to cable terminations, bus bracing and the windings of the upstream transformer. Use of the system demands calculating the risks of an arc flash damaging equipment without a bolted fault system against a bolted system damaging upstream equipment.
Since bolted fault devices have a significant likelihood of damaging upstream distribution equipment during operation, the industry has responded with innovative solutions that limit the peak fault current when a quenching device operates. These devices work by creating a low impedance current path using a controlled arc fault, not a bolted fault, which is fully contained inside the arc quenching device. The controlled path has a lower impedance than the original arcing fault, but higher impedance than a bolted fault, which limits the peak fault current. This results in a peak fault current that is at least 25% less than a bolted fault device, dramatically reducing stress on the upstream equipment while maintaining an equivalent, or improved, reduction in incident energy. Such devices are called current limiting arc quenching devices.
Arc quenching systems have the following sequence of operation:
– Arc Detection
– Arc Transfer
– Arc Containment
The immediate detection of an arc flash is necessary in order to send a trigger signal to the arc quenching device. Fortunately, arc flashes have typical characteristics that make them readily detectable. Arc flash relays can detect one, or a combination of the following arc flash characteristics:
– High Current
– Intense Light
– Erratic Voltage
– Pressure Wave
Most arc detection solutions on the market today detect the flash of light and rise in current present when an arc flash occurs. And while detecting both light and current is supposed to eliminate the risk of nuisance operations, it may not be sufficient in low voltage applications where a circuit breaker clearing a downstream fault can emit a visible flash of light. Therefore, in low voltage applications it may be necessary to interlock the operation of all circuit breakers with the arc flash relay to truly eliminate the risk of nuisance operation.
After the arc flash is detected, a trigger signal is sent to the arc quenching device to initiate the arc transfer. Arc transfer in arc quenching devices works according to Kirchoff’s Current Law. If a new current path with a lower impedance is introduced, the current will divide, and if that impedance branch is low enough the current reduces to the point that the unintended arc fault extinguishes.
After the arc is transferred, the energy must be contained. With a bolted system, the energy remains within the flow of current through the conductors and mechanically by conductor bracing. In comparison, with a current limiting arc quenching system, an arc containment vessel contains the energy in the form of a controlled arcing fault and therefore must be designed to handle immense heat and pressure until the upstream circuit breaker opens and de-energizes the lineup.
A final aspect when considering arc quenching systems is that they are electronic systems that require maintenance and testing. However, the newest systems are equipped with real-time monitoring of their own systems and functionality, known as system self-supervision. The ability to monitor the system in real-time is highly valuable and provides an added layer of confidence.
Current limiting arc quenching systems represent a revolutionary advancement and provides an alternative to traditional arc reduction and arc-resistant construction methods.
Eaton is a leader in arc flash safety and has recognized the industry need for arc quenching systems and has answered the call with the development of their Arc Quenching Magnum DS Switchgear.
Unlike other methods for arc energy reduction, Eaton’s Arc Quenching Switchgear does not require activation by an operator; the technology is active whenever the system is powered and can quench an arc fault in less than 4 milliseconds. Additionally, the arc quenching system can be used with other arc flash safety solutions, including zone selective interlocking, Arcflash Reduction Maintenance System technology or when included in traditional arc-resistant construction, to create a layered approach to safety.
Eaton’s Arc Quenching Switchgear also provides arc-resistant protection without the need for ducts, plenums, venting into the room, or special enclosure construction. The design is meant to be safe during operation, providing arc flash protection even if feeder breakers are removed or equipment doors are open.
“Eaton’s Arc Quenching Switchgear provides a new and powerful method to advance both safety and equipment protection for low-voltage switchgear applications. This revolutionary technology enables equipment to withstand an arc flash event with little to no damage which greatly minimizes downtime,” noted Dave Matthews, a marketing product line manager at Eaton Canada. Dave also noted that “this technology builds on decades of Eaton’s arc flash safety innovation, delivering best-in-class protection to enhance safety through innovations and services such as our Arcflash Reduction Maintenance System technology, arc resistant switchgear assemblies, arc flash studies and hands-on training programs.”
To sum up, arc flash is a danger faced by many in the electrical industry but a combination of training, best practices and the utilization of modern technology, such as current limiting arc quenching systems, can minimize damage to equipment and worker safety.
For more information HERE