How the IIoT Is Delivering on Asset Performance Management, Part 2
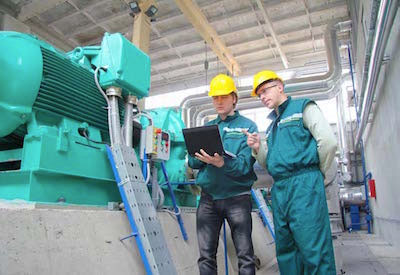
Oct 23, 2017
By John Boville
Part 1 of this 4-part series introduced ways in which increasing digitization might improve plant operations. Here in Part 2: how IIoT can improve the productivity of reactive, preventive, predictive and proactive maintenance.
Reactive maintenance, in which things aren’t fixed until they break, is probably the most widely applied maintenance strategy. According to ARC, this is especially true for non-critical assets in which the overall impact of failure is minimal. While reactive maintenance does not add costs in the short term, it can potentially contribute to higher lifetime costs, including the cost of diagnosing, fixing, testing, etc., as well as the cost of downtime during the operation. IIoT, however, can improve reactive maintenance by enabling a more efficient, more informed response.
“I’ve heard estimates that a field operator spends only 2.5 hours of a 10-hour shift on work that adds value to the business, while the rest is taken by looking for information — probably travelling back and forth to a central maintenance office presumably searching filing cabinets looking for service manuals, along with admin work and various other non-value add tasks,” says Greg Conary, Schneider Electric Senior Vice President for Strategy.
In a more connected environment, on the other hand, maintenance engineers or technicians could be sitting in front of their computers when an alarm goes off in the middle of the plant. Instead of taking the time to travel to the plant, they can view a supervisory screen that will alert them to the condition. With a click they can see the documentation and review the code that might be managing a flagged pump without leaving their desks. They could then connect to the PLC that is managing it; see what is going on within the actual program of responses; and determine whether it is a programming issue, a hardware issue, or whatever. If it is a broken pump, for example, they might be able to configure it from their desk. If parts are needed, they would have instant access to spares inventories or a simplified ordering process.
The limitations of preventive maintenance
Preventive maintenance has been shown to reduce maintenance costs over the lifetime of the asset, but has its limitations. Preventive maintenance is based on the assumption that assets deteriorate at predictable rates based on age and utilization, which is valid. But ARC points to U.S. Navy research showing that only 18% of equipment failures result from aging equipment. While IIoT may improve tracking scheduling and other aspects of preventive maintenance, it won’t necessarily address 82% of the other failures that result from seeming random operating events. These require condition monitoring based on analysis of more complex variables, which is what the IIoT promises to enable.
Delivering on the promise of predictive and proactive maintenance
Predictive and prescriptive (sometimes called proactive) maintenance strategies stand to gain the most from IIoT. In both approaches, process data is monitored to identify trends and issue alerts prior to failure. Predictive condition monitoring, as defined by ARC, is most appropriate for simple systems, where single variable math can be used to predict failure. More complex systems involve prescriptive condition monitoring, where multiple variables are analyzed to predict failure. This requires a more contextually driven understanding of operating conditions and providing more accurate diagnosis of the pending issue with fewer false positives.
Envisioning the possibilities is Thorsten Pötter, Ph.D., head of business intelligence and data management for Bayer and leader of the Industry 4.0 caretaker group for NAMUR, a user-driven consortium that provides best maintenance practices guidance for the chemical industry: “The device learns from the past, but also receives information from the current operating environment, such as temperature and humidity. What would happen if the device were to tweet all this information, regardless of who would be the recipient of this information? Could not you go a step further and gather this information and use it to help you evaluate models? This could significantly increase the quality of predictions of imminent faults in field devices and other components in the field,” he said at NAMUR’s 2013 general meeting.[1]
The advanced data historians and advanced analytical software needed to deliver the potential of IIoT are already in place to help process the deluge of operating data that could be flowing in. Today’s enterprise data historians can collect data for analysis and report on asset operations, health, maintenance, and regulatory compliance. They can collect continuously streaming time-series data from critical control, monitoring, and smart devices and then archive this data – increasingly in the cloud using advanced storage and compression technologies.
Ash Grove Cement, of Overland Park, Kansas, for example, uses Schneider Electric’s Avantis asset management software to automate maintenance data collection at each of its nine facilities. They have a well-defined enterprise asset management process to support equipment performance reliability, which improves production asset availability and utilization and provides a standardized solution for each production facility. The process and software enabled Ash Grove to reduce its inventory costs by US$2 million in the first year of implementation, while ensuring compliance with the EPA’s Portland Cement Maximum Achievable Control Technology regulation, thereby minimizing the potential loss of US$3 thousand per hour for every hour the kiln is offline.[2]
Delivering on the promise of predictive and proactive maintenance
IIoT makes it possible for more companies to achieve measureable benefits such as those that Ash Grove achieved, while extending the possibilities as well. It enables the real-time collection of data on the system operation, which can extend the lifespan of any asset and reduce capital expenses. Improved operating data helps capture the knowledge of experienced workers, which flattens the learning curve for new hires and helps minimize unplanned downtime.
Part 1 introduce ways in which increasing digitization might improve plant operations. Read Part 1 here: https://electricalindustry.ca/latest-news/3511-maintaining-the-iiot-how-the-iiot-is-delivering-on-the-promise-of-asset-performance-management-part-1. Parts 3 and 4 will explore five trends around IIoT that will help companies achieve maintenance benefits, and how IIoT is already improving operational profitability.
John Boville is a marketing manager for Schneider Electric’s marketing and innovation group, where he focuses on the Modicon controller line. He has been with Schneider Electric industrial automation for more than 25 years, including implementing market segment strategies for the automotive industry. Prior to joining Modicon, before it became part of Schneider Electric, he served for 12 years in project engineering for CEGELEC Automation as an industrial system designer, installation specialist, and project leader for large automation migration projects. He holds a B.S. in electrical engineering from the University of Bradford, U.K. Keep up with John’s latest insight in his blog: http://blog.schneider-electric.com/author/jboville/
Photo source: Schneider.