Transformer Short Circuit Considerations
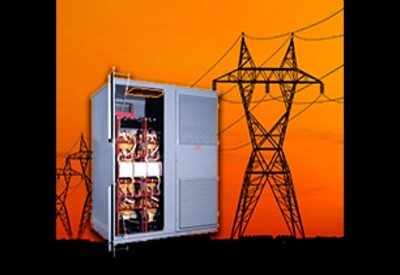
March 9 2016
Short circuits or faults can and do occur on electric power and distribution systems. When a fault occurs on the load side of a transformer, the fault current will pass through the transformer. As components on these systems, transformers need to be able to withstand these fault currents.
Fault currents flowing through transformers are significantly higher than the rated currents of the transformers. In a worst case scenario, the current would be as high as the current that would flow if system voltage was applied to the primary terminals while the secondary terminals are shorted — limited by the transformer impedance only. These currents produce both mechanical and thermal stresses in the transformers.
Photo credit: Hammond Power Solutions
Forces resulting from the currents passing through the transformer act on the conductors. The forces are a function of the peak asymmetrical current (the highest peak value of any cycle of the current), which is usually at its highest during the first half cycle of the fault. The duration of the fault is not normally a concern for mechanical withstand because the peak value of each cycle of the current reduces as the fault persists. The transformer manufacturer needs to ensure these forces do not damage the transformer.
The thermal stress is caused by the high current causing heating in the transformer. Both the RMS symmetrical current magnitude and duration of the fault contribute to the heating of the transformer. The transformer manufacturer needs to ensure the components of the transformer do not become hot enough to be damaged.
General purpose dry type transformers are typically designed to withstand the mechanical and thermal stresses caused by a short circuit occurring on the secondary terminals of the transformer with rated voltage applied to the primary terminals for a maximum of 2 seconds, provided the current does not exceed 25 times rated current. The fault current magnitude is a function of the transformer impedance. The table below shows the fault current for selected impedances and applies to both line currents and phase currents.
Transformer Impedance | Fault Current (times rated) |
4.0% | 25.0 |
5.0% | 20.0 |
6.0% | 16.7 |
7.0% | 14.3 |
8.0% | 12.5 |
The maximum of 25 times rated current is listed so that transformers with an impedance below 4% need only be able to withstand 25 times rated current, although the fault current could be higher than this. It does not mean that all transformers are able to handle a fault current up to 25 times rated current. With rated voltage applied to the primary a transformer impedance above 4% will not allow 25 times rated current to flow.
Many specifications indicate a fault level at the primary terminals of the transformer. Some customers will ask for a transformer to be braced for the primary fault level. A general purpose transformer is suitable to be connected to a system with the specified fault level, but the transformer impedance will limit the fault current through it to well below the available fault level. As an example, the customer requests a 2500 kVA transformer, 13.8 kV delta to 480Y/277 V, 5.75% impedance to be braced for 750 MVA fault level at 13.8 kV. In this case, the available fault current at the primary terminals is 31.4 kA. For a fault on the secondary side of the transformer, the transformer impedance will limit the fault current that flows in the primary to 1.8 kA in the lines and 1.1 kA in the coils — significantly lower than the available fault level. There is no need for the transformer primary conductors to be sized and braced to handle a 31.4 kA fault current.
Some operating conditions need special attention. Some customers specify the transformer to operate continuously with load at higher than rated voltage. If a fault occurs when the transformer is operating at higher than rated voltage, the resulting fault current would be higher than a typical transformer is designed for. This will increase both the forces in the transformer and the heating of the transformer. Some customers specify a fault duration longer than 2 seconds without specifying a higher voltage. This does not affect the forces but does increase the heating in the transformer. In these cases, a special design may be required.
One case in particular requires special attention: transformers directly connected to a generator. When a generator is supplying a load and the load is suddenly disconnected, the output voltage of the generator rises significantly for a short time until the excitation system decreases the voltage. If a fault occurs on the secondary of a transformer at this time, the fault current can be significantly higher than a typical transformer is designed for. Some applications may not have any overcurrent protection between the generator and the transformer primary winding, resulting in an increased duration. In such cases, it is recommended that IEEE C57.116 IEEE Guide for Transformers Directly Connected to Generators be reviewed to determine the short circuit withstand requirement for the transformer.
General purpose transformers have short circuit withstand capabilities that are sufficient for many applications. The transformer manufacturer needs to be informed of cases where a fault could occur on the secondary of the transformer when the transformer is supplied above rated voltage or the fault duration is longer than two seconds to ensure the transformer is suitably designed to withstand the possible secondary faults.
This document was first published as a white paper by Hammond Power Solutions, the largest manufacturer of dry-type transformers in North America. Hammond Power Solutions engineers and manufactures a wider range of custom transformers that are exported globally in electrical equipment and systems. The firm supports solid industries such as oil and gas, mining, steel, waste and water treatment, and wind power-generation.