Setting up an Electrical Safety Training Program: What’s Required by OSHA, CSA and NFPA?
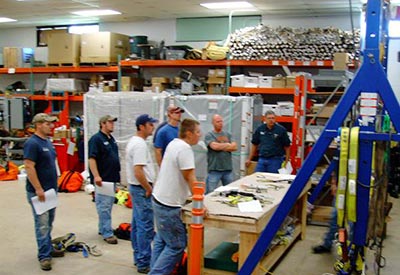
When putting together an electrical safety training program, what requirements does an electrical manager need to follow, for which employees?This first article in a two-part series helps to answer this question by looking at the level of training required, suggested components of a training program, and the definition of a “qualified” person. Watch for more in our May 26 issue.
CSA Z462,OSHA and NFPA 70E do not look at what a worker’s job title is.When determining what level of training is required, these requirements look at the hazards a worker may be exposed to.Any worker exposed to electrical hazards (that includes any electrical conductor or circuit part above 50 V) is considered a qualified person who needs higher level training.This may include many workers who do not consider themselves as electrically qualified, such as HVAC technicians, multi-craft workers, welders, and general maintenance personnel.
The purpose of electrical safety training is to ensure employees understand what is required of management and the worker when it comes to electrical safety.When employees face hazards that could injure or kill them, they are required to have a level of training that ensures they can recognize and avoid that hazard.
Building context
One method to determine OSHA’s intent is to read their Letters of Interpretation (LOI).These are OSHA’s responses to letters that people and companies have written, asking OSHA to provide more detailed explanations to specific questions and scenarios.They can be found on OSHA’s website (www.osha.gov) under standards.
Each LOI relates back toa particular section of the standard.One LOI concerns initial training for HAZWOPER (OSHA Hazardous Waste Operations and Emergency Response Standard). HAZWOPER training requirements are similar to electrical safety training, in that both sets of workers are exposed to hazards that could injure or kill.The OSHA LOI response sounds like a response to an electrical safety question.This particular LOI, which answers a question on computer-based (or similar) training, can serve as a best practice guideline for any jurisdiction.
OSHA states in the LOI, “Our position on this matter is essentially the same as our policy on the use of training videos, since the two approaches have similar shortcomings. OSHA urges employers to be wary of relying solely on generic, “packaged” training programs in meeting their training requirements. For example, training under HAZWOPER includes site-specific elements and should also, to some degree, be tailored to workers’ assigned duties.
Safety and health training involves the presentation of technical material to audiences that typically have not had formal education in technical or scientific disciplines, such as in areas of chemistry or physiology.In an effective training program, it is critical that trainees have the opportunity to ask questions where material is unfamiliar to them. In a computer-based program, this requirement may be providing a telephone hotline so that trainees will have direct access to a qualified trainer.
Equally important is the use of hands-on training and exercises to provide trainees with an opportunity to become familiar with equipment and safe practices in a non-hazardous setting. Many industrial operations, and in particular hazardous waste operations, can involve many complex and hazardous tasks. It is imperative that employees be able to perform such tasks safely. Traditional, hands-on training is the preferred method to ensure that workers are prepared to safely perform these tasks. The purpose of hands-on training, for example in the donning and doffing of personal protective equipment, is two-fold:
• to ensure that workers have an opportunity to learn by experience
• to assess whether workers have mastered the necessary skills
It is unlikely that sole reliance on a computer-based training program is likely to achieve these objectives.
Thus, OSHA believes that computer-based training programs can be used as part of an effective safety and health training program to satisfy OSHA training requirements, provided that the program is supplemented by the opportunity for trainees to ask questions of a qualified trainer, and provides trainees with sufficient hands-on experience.”
This LOI highlights four important requirements:
1. Training must be tailored to be site-specific and the worker’s duties
2. Initial training has to be interactive and effective
3. Trainees must have an opportunity to have specific questions answered immediately, not after some period of time
4. Training must be hands-on and have a demonstration of skills, 5. OSHA prefers instructor-led hands-on training
Identifying who is “qualified”
Here’s OSHA’s definition of a qualified person (29CFR1910.399)
“Qualified person. One who has received training in and has demonstrated skills and knowledge in the construction and operation of electric equipment and installations and the hazards involved.”
A qualified person must have:
• skills and knowledge of the construction of the equipment they are about to work on or operate, as well as how the manufacturer recommends that equipment be operated.
• skills and techniques to understand how the electrical system operates and the hazards associated with that equipment and system.
“Installations” refers to the type and configuration of the electrical system; main-tie-main, double-ended substation, breaker-and-a-half, ring bus, radial, etc. Each of these types of electrical systems has unique hazards that workers must understand.A qualified person must receive training in and demonstrate skills and knowledge in all the above.
For qualified workers (those who are exposed or may be exposed to electrical hazards) OSHA requires the following from 29CFR1910.332(b)(3), 1910.333:
“Qualified persons (i.e. those permitted to work on or near exposed energized parts) shall, at a minimum, be trained in and familiar with the following:”
1. Absence of voltage testing1910.332(b)(3)(i)
“The skills and techniques necessary to distinguish exposed live parts from other parts of electric equipment.”Interpretation – Qualified persons must be able to demonstrate testing for the absence of voltage.
2. Nominal voltage1910.332(b)(3)(ii)
“The skills and techniques necessary to determine the nominal voltage of exposed live parts, and” Interpretation – How is the system voltage determined before contact is made with energized circuits or conductor parts?
3. Approach distances1910.332(b)(3)(iii)
“The clearance distances specified in 1910.333(c) and the corresponding voltages to which the qualified person will be exposed.”Interpretation – What are the safe approach distance for a qualified person to exposed energized conductors or circuit parts?This would include not just the shock hazard, but also the arc flash hazard, now it can be calculated.
4. Safe work zone1910.333(c)(2)
“Work on energized equipment.” Only qualified persons may work on electric circuit parts or equipment that have not been de-energized under the procedures of paragraph (b) of this section. Such persons shall be capable of working safely on energized circuits and shall be familiar with the proper use of special precautionary techniques, personal protective equipment, insulating and shielding materials, and insulated tools.”Interpretation –
a) Proper use of special precautionary techniques refers to being able to set up a safe work zone around exposed energized conductors or circuit parts.
b) Use of personal protective equipment (PPE).This would include how to choose the PPE that would provide adequate protection, how to inspect it, how to wear it or use it, how to store it, how to care for it, what its testing requirements are (if any), and what its limitations of use are.
c) Use of insulated tools covers much of the same requirements for choosing, inspecting, storing and limitations of use.This is no small thing and there has to be some methodology of documenting that the qualified person demonstrated these skill and techniques successfully.
This article has been lightly edited. In Part 2: how CSA Z46 and, NFPA 70E compare by emergency response training, lockout/tagout and more. Also includes a handy checklist summary of CSA, NFPA and OSHA electrical safety training requirements.
James R. White is Training Director, Shermco Industries, Inc. for Fluke Corporation.