Improving Arc Flash Prevention and Safety
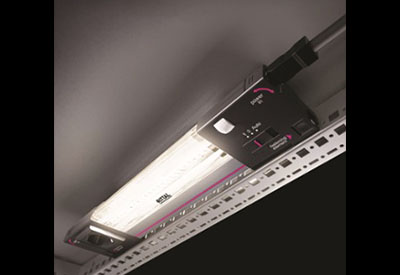
November 14, 2016
By Steve Sullivan
Working among the electrical components in an enclosure comes with inherent risks. The power in any one enclosure can range from 2kw up to 200kw depending on the power density. One of the most common and dangerous risks is an arc flash (or flashover).
When an explosive release of energy erupts from a phase-to-phase or phase-to-ground arc fault, the results range from devastating to deadly. This air to ground electrical explosion is a critical concern.
The destructive force of an arc flash
The dangers from an arc flash are all too well known. When metal expands and vaporizes at the fault, it causes extreme heating of the air, upwards of 10,000°C/18,032°F. The concussive pressure wave can knock personnel off their feet; the ultraviolet light flash can cause blindness; the sound blast, deafness; and the molten metal and heat can cause second and third degree burns. The specific death toll has been estimated to be up to 1-2 people every day worldwide.
An arc flash can result from unsafe work procedures, accidental contact, or more systemic problems such as corrosion of components and connections or insulation failure. Arc flash prevention should be incorporated into any application from the beginning of the design process.
Minimizing arc flash exposure
Design and retrofit approaches can limit exposure by using components installed outside the enclosure to permit qualified personnel in personal protective equipment (PPE) to service equipment inside without opening the enclosure door. Interface flaps and window kits permit data retrieval, equipment monitoring or routine maintenance to be performed from outside. Collapsible fold down shelves be raised for use with laptops and monitoring equipment. External data pockets can hold wiring diagrams, operation manuals and other documents.
Arc flash protection
Sometimes components must be accessed from inside the enclosure. For example, Rittal’s arc flash solution keeps high and low voltage equipment within the confines of their own respective enclosures. Low voltage enclosures house equipment that is used for programming, data acquisition and system adjustment.
High voltage components are isolated within their own disconnect enclosure, while line side power is segregated within the power isolation enclosure. A partition wall acts as a barrier to high voltage line side power. An interlocking door system ensures that the high voltage enclosure cannot be opened while the disconnect switch is in “ON” position.
For additional safety, all interlocked doors and master door must be closed in order to re-energize the enclosure. This removes potential for accidental contact with the inline power when the disconnect enclosure is put in a safe power-off position, and locked and tagged out.
Minimizing exposure to line side power can help protect personnel from accidents. A qualified person wearing PPE and following appropriate safe work practices can perform visual inspections and tasks, such as diagnosis, testing, troubleshooting and voltage measurement with the door open even when the main enclosure is energized.
Safety is always your priority, so download Rittal’s Arc Flash and How to Prevent it free whitepaper for the first step towards arc flash prevention: http://info.rittalenclosures.com/arch-flash-lp-0.
Steve Sullivan is a training manager with Rittal. This article was first published online as a blog: http://blog.rittalenclosures.com/blog/author/steve-sullivan-training-manager.