Power Factor Correction: An Overlooked but Powerful Tool for Delivering Energy Efficiency and Savings
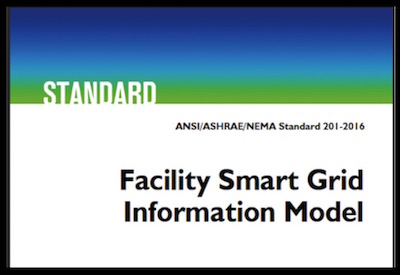
June 23 2016
Joy Silber
Amid all the talk about how to reduce CO2 emissions and limit climate change, renewable energy sources such as wind and solar often take centre stage. But there’s another technology poised to deliver energy reductions of 10% or more that gets far less attention: power factor correction (PFC).
If you’re not familiar with PFC, you are far from alone. To date, it’s been a largely overlooked method of reducing energy consumption, costs and CO2emissions, and achieving sustainability. But PFC is actually far more effective than many “green” alternatives because it effectively enables companies to get more power out of the same amount of utility electricity.
Understanding power factor
I won’t kid you: PFC is a bit complicated to explain and understand, making a full discussion of it beyond the scope of this post. You can learn all about it from this free Schneider Electric paper titled Energy efficiency improvement through optimization of the power factor correction.
But the basic concept is it takes more energy to power a given load than the actual power that the load consumes. That’s because some of the energy is lost in translation, so to speak. Power factor is used to determine just how much more energy will be required to power the load. This amount is measured by calculating a ratio that shows how efficient any given machine is. A motor with a power factor of .90, for example, is 90% efficient. To determine how much energy you’ll need in kVA to power that machine, you perform an equation: 100 (for a 100kW motor) ÷ 0.90 = 111kVA. So you’ll need 111kVA of utility power to run that 100kW motor.
Saving energy with power factor correction
Obviously, the lower your power factor of a given piece of equipment, the less efficient it’s going to run. And that inefficiency can cost you more than just a higher utility bill because in some areas, you’ll get penalized for consuming more power than your contract allows, taking into account your power factor.
The key to ensuring that doesn’t happen is to use a capacitor bank or energy compensator. These systems perform PFC to help reduce the amount of power an AC device has to consume to generate its rated amount of power. Some systems, such as Schneider Electric’s VarSet low-voltage capacitor banks, automatically correct power factor. This results in a power factor close to 1, meaning virtually no power is wasted.
Using PFC systems can deliver a number of benefits, including:
• significant savings on electricity bills, with ROI typically within two years (actual savings vary depending on local utility penalties)
• improved energy efficiency
• attained sustainability goals
• reduced energy use waste
• increased available power at your facility
• reduced carbon footprint
• Improved equipment reliability and lifespan by filtering “dirty power”
Sounds an awful lot like many of the same benefits that solar and wind deliver, doesn’t it? The savings can indeed be impressive, and they’re relatively simple to achieve. To learn more about power factor correction in your facility, email:powersolutions@schneider-electric.com
Joy Silber is the Strategic Marketing & Sales Optimization Manager of Power Solutions at Schneider Electric. With experience across multiple industries: Food and Beverage, Mechanical, Agriculture and Power Transmission, Joy has held previous roles in National Sales Development, Market Segment Management, Marketing Services Management and Business Development. She has a B.S. from North Carolina State University and is an active volunteer in her community. This article was first published as a blog