6 Myths About Balancing
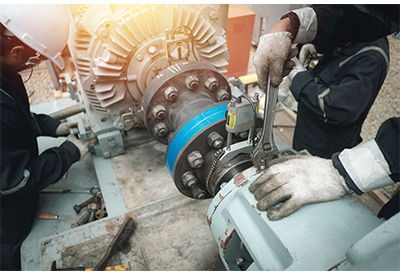
Aug 18, 2019
If you are lucky, there will be a veteran in your shop that will pass their knowledge of good machining practices on to all the rookies who come aboard. Most of the knowledge they possess will be priceless, but there are a lot of myths about balancing floating around out there. Teaching these myths to new recruits who don’t know any better can cost your operation a lot of lost time and money. In this article, we will address these misperceptions and offer a more factual view of best practices for balancing toolholder assemblies.
Myth #1: Balance Doesn’t Matter that Much
Balancing has become an industry standard best practice, and if balancing is a standard then how could it not be important? Let’s look at some examples. Cutting tool manufacturers balance wheel packs prior to grinding. Toolholder manufacturers pre-balance the holder after production. Many machine tool builders insist on balanced assemblies (ISO1940-1: G2.5 at maximum RPM) to maintain warranties on their spindles. Leading aerospace/aircraft and automotive manufacturers in the US inspect the balance of every tool assembly prior to beginning production. These are industry leaders who definitely think balance matters. If you’d like to follow their example, we can help.
Myth #2: Balance is Only Necessary at High Speeds
Balance matters at any speed. Just because you cannot hear or see immediate evidence of imbalance does not mean that it isn’t there. It will eventually reveal itself, and it won’t be good. It will show itself over time as wear on spindle bearings, faster deterioration of cutting tools, and failures during machining that can’t be easily identified. Imbalance always has negative consequences. Consider your car, you balance your tires for better wear and performance, so why wouldn’t you do the same with your toolholder assemblies?
Myth #3: Pre-Balanced Holders Are “Good Enough”
Having a toolholder come pre-balanced might seem like it’s saving you a lot of work, but most of those are balanced without any mating components. Things like retention knobs, collets, collet nuts, bearing cages, hydraulic fluid and cutting tools are often ignored as non-impactful “variables”. But these items have a significant effect on balance. It all depends on the holder type and taper, but the balance you think you’re getting versus what pre-balanced toolholders actually deliver are most likely two different things.
Myth #4: Good Runout Accuracy = Good Balance
Runout and balance are two different things. But while imbalance can certainly create runout during machining (where none was measurable statically) improving runout accuracy will actually have zero impact on the balance of the toolholder assembly. To optimize your process, you need both runout accuracy and proper balance.
Myth #5: Dressing A Grinding Wheel is the Same as Balancing It
Dressing might clean and renew a grinding wheel and bring it back to its original shape, but it does nothing to correct the weight imbalance that can stem from a variety of reasons. A perfectly round wheel does not necessarily mean a perfectly balanced wheel. Think of your car again, this is the same reason that your tires need to be balanced.
Myth #6: Balancing in House is Too Expensive
Investing in the proper balancing tools might seem too expensive at first glance, but without the savings that having properly balanced tools provides it might actually be costing you more not to balance. Most shops that perform balancing in-house see ROI on their investment in 18 months or less.