Paper Mill Migrates to Modern DCS
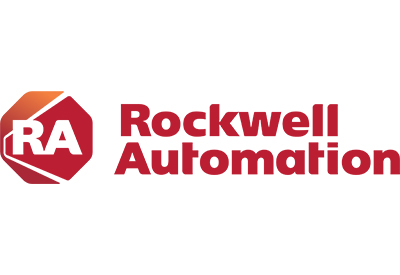
Dec 2, 2019
By Randall Fischer
When is the best time for downtime?
For most, the answer is, “No time is a good time.” The real question becomes, how long can your aging DCS limp along before an upgrade is unavoidable?
Today’s pulp and paper mills operate under constant pressure to reduce production costs and increase yields. “If it isn’t broken (yet), don’t fix it,” is a risky approach and with any legacy system, and especially a DCS that has seen more productive days.
That’s what we found with a customer relying on an aging pulp batch digester. This is the most complicated process in the pulp mill – problems here create problems everywhere.
Is it time?
As with most older systems, this customer – a producer of specialty food wrappers for quick service restaurants – faced significant issues around the lack of spares, obsolete equipment support resources and process visibility. Operators were forced to manage batch cooking processes from various stations and views, with no single source of truth.
The inefficiency of their legacy DCS now outweighed the downtime risk of migration.
Single pain of glass
The new batch digester control was designed to:
- Improve digester turnover, including undercooked rejection reduction and uniform Kappa
- Improve digester temperature control during the cook
- Reduce steam use during pre-steaming of chips during loading
- Increase turpentine yield
In addition to achieving these goals, upgrading the DCS resulted in a significant benefit for the workforce: operators now have all of the information needed in one system via a “single pane of glass.”
Decreasing DCS skills gap increases consistency
Operators already familiar with our PlantPAx® DCS for other process easily converted their knowledge for this niche application – saving training time and reducing the impact of a skills gap, or the lack of knowledgeable people available to learn and manage the new system.
The batch digester control now can adjust the cook of the pulp based on several factors including outside temperature and moisture, optimizing each cook by making improvements automatically for more consistent results. This digester optimization, coupled with standardized operation on every shift (regardless of operator), has resulted in the anticipated result – a reduction in downtime – as well as improvements in product quantity and quality.
Bottom-line: they produce more batches per day, with fewer bottlenecks.
While this is a niche application, the benefits achieved can apply across other process industries: operators have an easier time handling the system and have greater visibility into the processes; executives realize the promised gains for increased production and improved yields – and more.