Engineering More Reliable Electrical Systems in Wastewater Treatment Plants
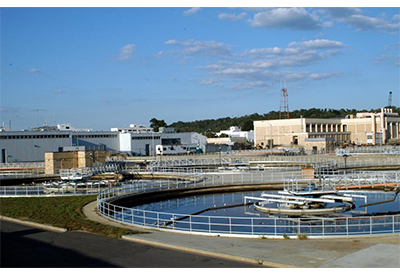
October 28, 2022
By Jim Medeiros, Account Manager, Appleton | Emerson
Maintaining wastewater treatment plants is essential to meeting the critical need for clean water. In the United States alone, about 34 billion gallons of wastewater is processed each day. Much of this can be attributed to increasingly stringent, but environmentally necessary, government regulations that now require companies processing chemicals, pesticides, and other harmful materials to recover ninety-five to ninety-nine percent of water from waste streams before releasing it back into the environment. Other factors contributing to mounting demand are global population growth, rapid urbanization, and the expansion of farming operations.
Climate change has compounded the problem by disrupting hydrological cycles, and increasing the severity of floods and droughts. If that wasn’t enough, the water crisis is further complicated by the aging of America’s 16,000 wastewater treatment plants. The majority of plants in the United States were designed with an average lifespan of 40 to 50 years. Plants that were constructed in the 1970s, around the passing of the Clean Water Act in 1972, are reaching the end of their service lives and require massive overhauls. The Environmental Protection Agency estimates that roughly $271 billion in infrastructure will be needed over the next 25 years to maintain and improve the country’s ailing water facilities.
Electrical equipment makes up a large part of that infrastructure. Massive amounts of electricity are consumed in the of processing of wastewater. In fact, approximately 4 percent of US electricity usage is linked to water treatment, corresponding to 30.2 billion kWh per year. While electrical equipment largely operates behind the scenes at wastewater treatment plants, it has become progressively more important as demand for clean water continues to spiral. Unfortunately, due to corrosion and chemicals, wastewater treatment plants present an extremely hostile atmosphere for electrical equipment, causing deterioration and forcing costly repairs and expensive replacements. Constant upkeep of equipment is required to prevent premature failures that can result in mass water shortages.
Because electrical equipment must provide absolute reliability in wastewater treatment plants, you need to be aware of the three features that have proven critical to it long-term performance and safety: Corrosion Resistance, Hazardous Location Ratings, and High Energy Efficiency. Below we address each.
Challenge 1: Corrosion
The greatest threat to metallic electrical products is corrosion. Conditions are even worse when the plant is located in a humid coastal area exposed to salt spray.
Corrosion in wastewater treatment plants comes in many forms. Filiform corrosion, for example, is induced by pinpoint penetration by moisture. Common chemicals found in treatment centers also severely attack metal, including ferric chloride, chlorine, acids, and alkalis. The interaction of components of sewage will produce secondary chemicals with even more toxic and corrosive properties, leading to the faster destruction of metallic surfaces and even concrete. Hydrogen Sulfide (H2S) or “sewer gas” is another threat to metallic components, causing so many corrosion problems for wastewater treatment facilities that it warranted an EPA warning. Simple “fatigue” corrosion occurs in ductile metals, resulting in cracking or breaking. Bacteria in wastewater will attack metal components, leaving them vulnerable to corrosion by sulfuric acid.
Of course, the outdoor environment exposes metal components to corrosion as well. Electrical components such as lighting fixtures mounted outdoors are put into jeopardy by rain, snow, UV rays, salt spray, and wide temperature fluctuations, in addition to the aerosols from settling tanks and outdoor chlorination. This type of corrosion, known as atmospheric corrosion, accounts for more material failures, from both a tonnage and cost perspective, than any other.
Since this isn’t a perfect world, we can’t eliminate corrosion. But its destruction can be greatly limited. Here’s how:
1. Use corrosion-resistant products. For corrosive and high-humidity environments, the first line of defense is material selection. Aluminum or stainless steel enclosures are generally accepted materials. In extreme conditions, fiberglass-reinforced polyester enclosures may be necessary in lieu of metal construction.
2. Specify a protective finish. When an application calls for devices with the high tensile strength and ductility of malleable iron, the best, most cost-effective way to combat corrosion is to choose a coating that effectively seals out water, chemicals and other corrosive contaminants. Paint alone is rarely enough. A more durable choice is a triple-coat finish comprised of a zinc plating, chromate dip, and electrostatically applied epoxy powder coating.
3. Control the environment. As much as possible, shelter electrical installations from the weather and corrosive chemicals. Eliminate industrial contaminants from the air through ventilation and keep fuel-burning equipment in good repair to minimize emissions.
Challenge 2: Hazardous Locations
The majority of pumping stations, closed spaces, and buildings that make up wastewater treatment plants must be considered hazardous locations. Decomposition of waste generates methane and hydrogen, both of which are potentially flammable gases if an electrical or other source of ignition is present. Chemicals used for purification may also be potentially flammable, namely hydrogen peroxide and chlorine dioxide, even in relatively low concentrations.
Electrical products installed in these areas must be rated for use in hazardous locations per the National Electrical Code (NEC). The NEC references NFPA 820 when classifying hazardous locations in wastewater treatment and collection facilities. According to NFPA 820, electrical systems associated with screenings removal facilities, wet wells, and dry wells need to be designed on the basis of a Class I hazardous location. The application of proper ventilation and monitoring may allow the electrical hazard classification to be made less stringent i.e., Class I, Div. 2 or to “unclassified.”
Challenge 3: Energy Efficiency
Faced with higher operational costs and tighter budgets, energy efficiency has become a top priority within the wastewater sector. Facility operators and governments alike are ramping up efforts to reduce energy costs and improve environmental performance. In particular, they are focusing on lighting which can constitute 25% to 40% of a plant’s electrical usage and makes up a significant portion of its total energy bill.
Traditionally, wastewater facilities have used three types of high intensity discharge (HID) lighting: High-pressure sodium (HPS), metal halide, and mercury vapor lights. Laws were enacted in 2007 prohibiting manufacturers from producing and selling mercury vapor lamps and high-wattage metal halide ballasts. Retrofitting existing HID lighting with energy efficient LEDs, combined with photocells, occupancy sensors, and dimming capabilities, can reduce lighting’s energy draw up to seventy percent. Along the way, it can also decrease CO2 emissions by sixty-five percent. As an added bonus, LEDs offer “instant on” capability, even in extremely cold temperatures, eliminating the prolonged warm-up time associated with HIDs. Installing LEDs may also qualify the plant for a rebate incentive from its local energy provider.
Final Thoughts
Every stakeholder in the wastewater treatment industry has a tremendous responsibility to the local community with regards to water safety, availability, and sustainability. One way to ensure the continuous flow of clean water is by installing electrical products specifically designed for these environments. By specifying electrical equipment that is corrosion-resistant, properly rated, and energy efficient, engineers can ensure plants run without time-consuming maintenance, even in the most difficult, heavily loaded industrial and municipal sites.
Go HERE for more information