Shaping the Future of Manufacturing: ABB’s Investment in Automation and Growth at Pointe-Claire Facility
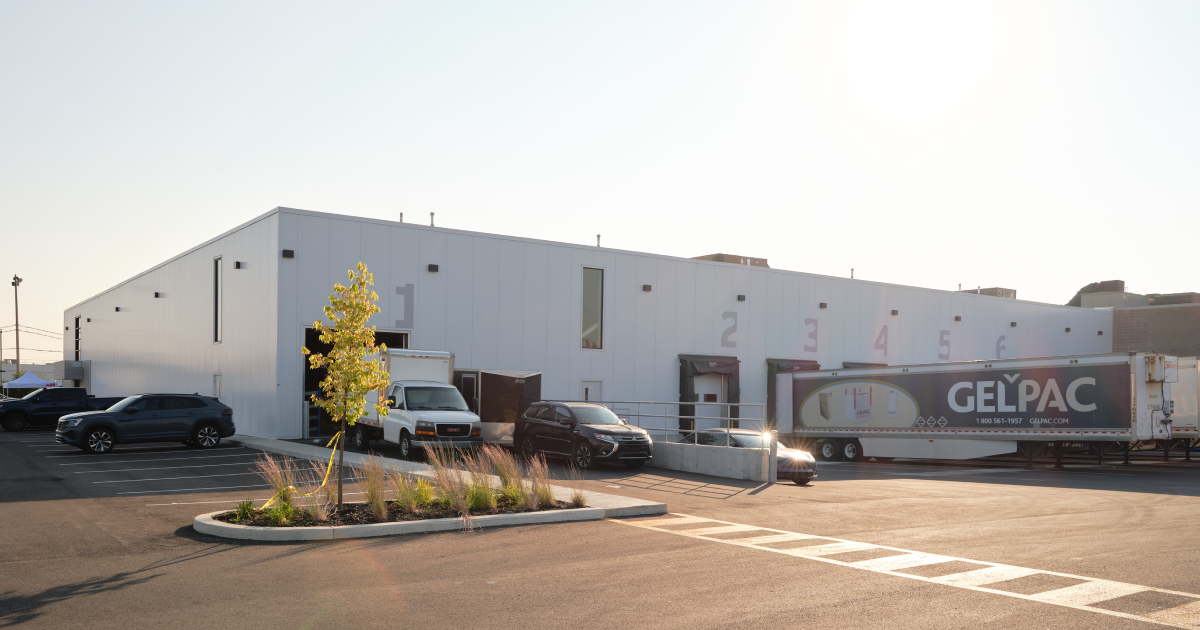
March 28, 2025
By Elle Bremmer
During my visit to ABB’s facility in Pointe-Claire, dubbed T-CAN after its location alongside the Trans-Canadian highway, I saw firsthand how automation is shaping the future of manufacturing. Specializing in plastic injection molding, the plant produces key products for ABB, such as their Marrette wire connectors, NuTek thermoplastic boxes, and Carlon plastic fittings, with impressive speed and precision.
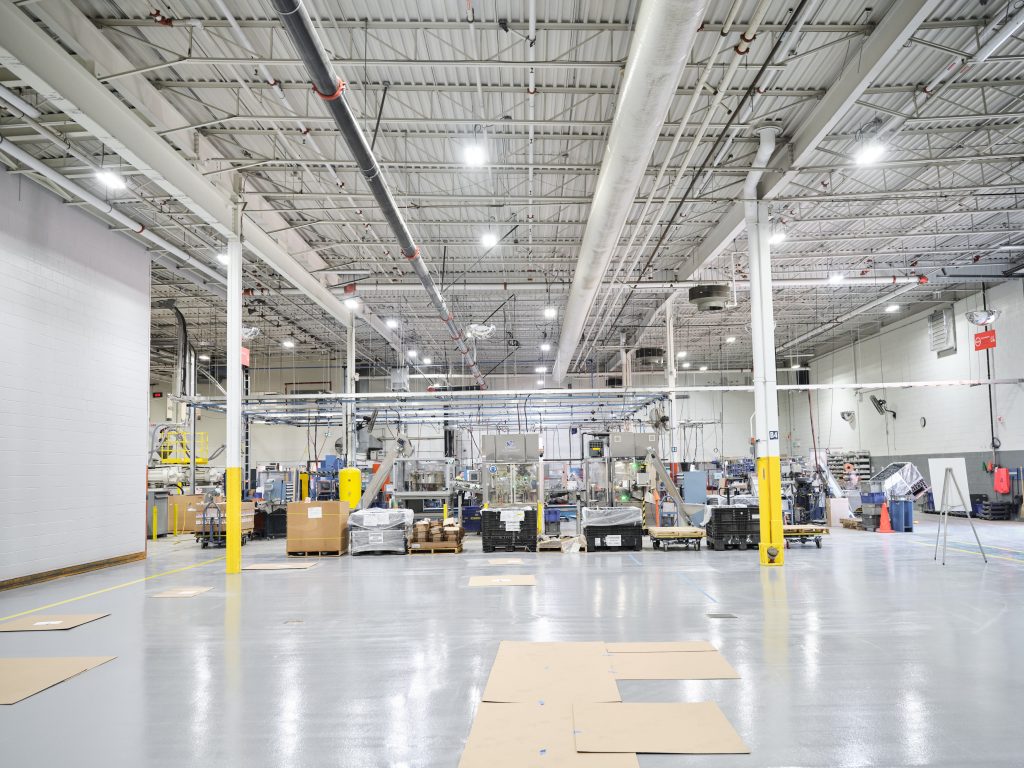
In 2021, ABB decided to make a significant investment in the T-CAN facility, pouring CA$16 million into its Installation Products Division.. This investment reinforces the company’s commitment to keeping the production of these Canadian legacy products on home soil, ensuring the long-term sustainability of jobs and manufacturing in Quebec. This expansion was completed in late 2024, adding over 40 new full-time jobs to the region and increasing square footage by 30,000 square feet. The expansion comes on the heels of a broader global investment from ABB at US$165 million from 2020, which included advancing robotics and digital technologies, along with regionalizing production.
Danny Coté, Regional Operations Leader at ABB with 25 years of experience, guided me through the facility, showcasing its operations and technology. Coté shared that ABB’s vision for the Pointe-Claire facility is one of growth, stating that with the expansion, “we have room to grow and room to play.”
With a planned workforce of 80 employees by the end of this year, the facility is poised for further expansion.
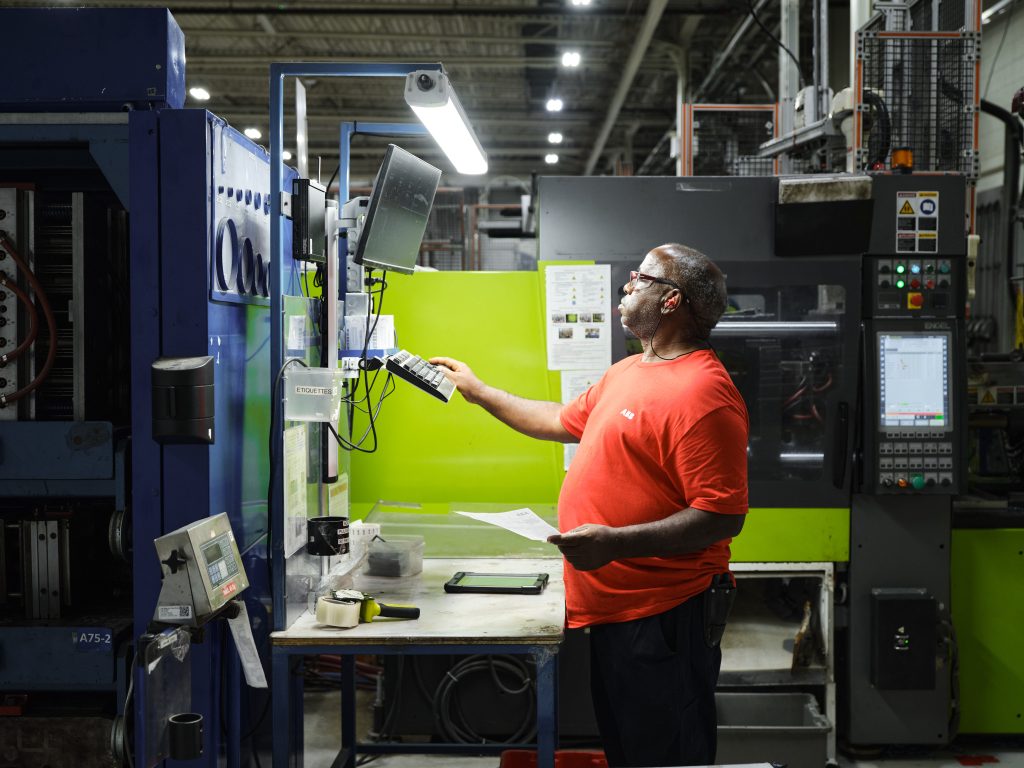
Automation technology serves as the backbone of innovation at the facility, transforming the way work is done. During the tour, I was introduced to two of ABB’s collaborative robots, or “co-bots,” which are revolutionizing the way work is done on the plant floor.
Samuel Huynh, an automation engineer at the facility, explained the function of these co-bots. “It allows us to collaborate with an operator to complete tasks with more efficiency and ease,” he said.
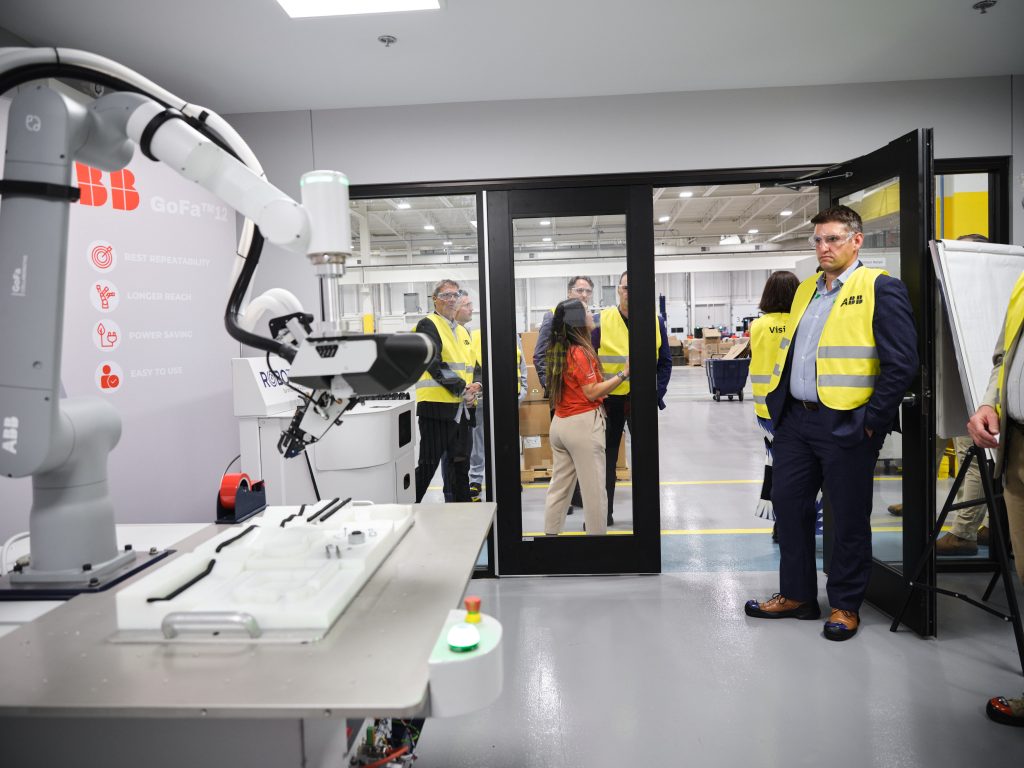
The co-bots have been integrated into various tasks, including adding labels and placing parts into packaging which serves to reduce the manual strain on employees. “The goal is to automate repetitive tasks,” Samuel explained.
The first co-bot, named ‘Wall-E’ by an employee vote after the character in the Disney Pixar film of the same name, picks a randomly placed part from a conveyor when it comes out from the injection press. Samuel describes some of the difficulties of developing a piece of technology like Wall-E. One challenge was in developing the vision systems, which had trouble with light reflections from a part, interfering with the sensor recognition. Fortunately, ABB Robotics provided support to resolve this problem. Samuel gives me a demonstration of Wall-E, challenging it by holding the part, a thermoplastic box, in different ways to challenge the co-bot’s vision system. The arm takes a moment or two to scan but is able to find its bearings and complete the task at hand.
Afterwards, I meet ‘Eve,’ the second iteration of Wall-E. Like Wall-E, Eve is a one-armed robot, but it had a longer reach. Its main application is for deep bin picking tasks. The development and optimization of Eve took approximately 8 months, and Coté tells me the goal in the future is to have a co-bot available at every workstation. But this development will take some time to implement.
I asked Samuel how employees responded to the implementation and integration of these co-bots on the plant floor. “Overall, it has been a big success,” he tells me.
There have been training activities to familiarize employees with the co-bots, and while he admitted that there was a bit of a steep learning curve, employees are now excited to work alongside the new technology. He emphasized that “the goal was and is always to keep employees on,” noting that the new technology complements the human workforce rather than replacing it.
Coté and I continue our walk through the facility, and we stop to take a look at what appears to be fittings being molded and cut, hot off the press, before being dropped into a cooling system. Coté emphasizes elements of sustainability at the facility, explaining to me that the leftover plastic is sorted out and able to be re-used, ensuring no waste.
We then move to another corner of the building, now looking at the development of ABB’s Marette wire connectors. The machines produce the product at an extraordinary rate of 200-300 parts per minute. Coté highlights a challenge unique to the connectors: ensuring that the springs inside the wire connector stay upright while producing large quantities at a fast pace.
We look towards a vibratory feeder, and the conical copper springs fall into position, ready to be placed into the plastic component of the wire connectors. Watching the parts come together and exit into a bin, Coté tells me that developing the technology for this facility took a great deal of time and effort. ABB collaborated with two local systems integrators, Génik (based out of Saint-Jérôme) and CFM (based out of Sherbrooke) to ensure the smooth integration of the technology into existing workflows.
Looking to the future, ABB’s Pointe-Claire facility is set for growth. Coté anticipates business to double by 2028, making the continued development of cutting-edge technology and skilled labour a crucial part of its strategy moving forward. As the facility expands and technology evolves, ABB is positioning itself for continued growth, driving the future of manufacturing in Quebec.