Managing Change: Sones
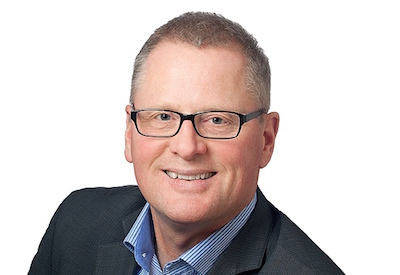
Mar 26, 2017
By Keith Sones
When I first graduated as an occupational safety and health technologist in 1991, I was on a mission to save the world. Armed with my newfound knowledge, I recognized the flaws in the industrial complex and was bound and determined to change everything.
Day 1 on the job. One of my first assignments was to deliver a technically demanding safety training program. The issue of confined space entry was (and still is) critically important for employees to understand and to execute properly. For those readers who may not be familiar with the topic, work is often required to be performed in locations where the air may become toxic or oxygen deficient, and rescuing a worker in trouble is logistically challenging. Examples include vessels, the hold of a ship, manholes, underground pipe, and other similar hard to get to places.
The training process at that time included presenting a series of slides using my portable overhead projector. PowerPoint and other presentation tools had yet to be developed, so my take on it was to use black text on a clear background so it was easy to see. I even threw in a few pictures to liven things up a bit — I had indeed impressed myself.
It only took a few training sessions, during which I singlehandedly managed to lull an entire audience to sleep, to realize that however impressed I was with myself, those on the receiving end of this “training” didn’t share my enthusiasm. Dejected but determined to find a way to do things better, I put my thinking cap back on. What was it that I missed so significantly? What did a better mousetrap look like? How could I move past the point where the only reason employees showed up to a training course was for the free coffee and doughnuts?
And then — eureka! I had it! The light bulb went on as I thought about some of the training I’d received myself. The good instructors always went the extra distance to show me what to do and have me practice. Admittedly, I had enjoyed several in-session naps at the expense of less than skilled teachers who insisted that it was really important to tell me every bit of information I would ever need to know through the use of endless text books and blackboard space. Most of those classes were forgotten the next day. I could, however, easily remember how to tie my shoes (aged 4, when my mom showed me) or dissect a frog (thanks, Mr. Jones). I had to show people, not just tell them. I would build a confined space on wheels.
Working with industry professionals and construction experts, I drove forward to arrange a facility design and a training curriculum. When finished, the mobile unit had the ability to force oxygen out of the space while the students could safely test the air. Imagine being able to look at what appeared to be a perfectly good room full of air, then have the test equipment show you that would be unconscious within seconds. It was a pretty powerful lesson. (Note: even today, the majority of confined space deaths are those of would-be rescuers, running into a space that looks safe to rescue a downed colleague.)
It was at this point I became the student in a class lead by a professor named The Human Condition. Having access to a state of the art new training tool should have elated my fellow safety training practitioners. I fully expected there to be a line-up at my door of bright eyed trainers fighting each other to get to the keys so they could provide new and improved guidance to their employee groups.
And that just didn’t happen.
I found myself having to push people to even take a look at my new brainchild. “Cool idea, Keith, but I’ll use the old materials,” said some. Others decried the cost of moving such a unit to their location, while still more suggested, “Maybe I’ll give it a try next year.”
To say I was shocked is an understatement. Why was everyone so resistant? Come on now, I thought, this is soooooo much better than what we’ve done before.
What did I miss? Why didn’t they see the value? All I knew at that time was that I spent several nights laying awake, worrying that I’d done the wrong thing and my manager would be doubting the trust he’d put in me. I was sure I’d be fired.
The answers came to me through a seasoned mentor that had worked with me throughout the development of the shiny new (and now underutilized) training trailer. He was edging towards retirement and had observed a lot over his many years. “It’s a fantastic thing you’ve got here”, he told me, “and it will catch on once people see someone else test drive it in a few training sessions. Mostly, they want to see what the students, and most importantly their managers, have to say about it. What they are doing now is predictable. Boring classroom training might not work nearly as well, but everyone knows the process and can say they have checked the box on the annual training plan.”
OK, I gotta admit I hadn’t seen that one coming.
Over the next few years, reality lined up with my original theory and using the new unit became the default method of training throughout the company. I was pretty proud to see that evolution, and in retrospect, my naïve enthusiasm was probably well placed since I might not (actually, probably not) have even attempted such a venture if I’d been around the block a few more times.
Since that early experience, I’ve made a habit of looking for signs of this resistance, and it’s everywhere. The advantage I have now is a better understanding of why people fight what seems to be an obvious benefit to them, at least from the outside looking in. Most often, it’s a simple matter of being scared. Fearful that we might make a choice that works out poorly, and our family/friends/colleagues will judge us. You know, the whispers in the hallway of “He’s that guy, the one that tried to get us to use the new product. The one that failed in the initial tests. Thank goodness we didn’t listen to him.” Or, you might have a performance bonus geared around doing things the old way, so there is no way you’re going to change things up now. Many organizations tell us to take measured risks as a path to finding better ways of running the business, but personal experience may tell you that taking risks is a certain path to career doom.
So, what to do when that light bulb in your head flashes up a new idea? Think about it, investigate it, ask others, and if the objective evidence says it’s worth pursuing, do it. The results are worth the hard work and angst that come along with pushing your idea through the forests of worry and peer malaise. Not only will you have made your place of work safer, more efficient or more profitable, the accomplishment feels good. It really does.
And since I learned that lesson early, I’m quite eager to tell you about a way you can save significant money on projects and get them done faster. I know, I know, sounds too good to be true. But that’s for next time.
Keith Sones is Vice President, National Business Development, The Valard Group of Companies.