Crop Nutrition backed by Saskatchewan’s Potash Mines and Rittal’s HD Enclosures
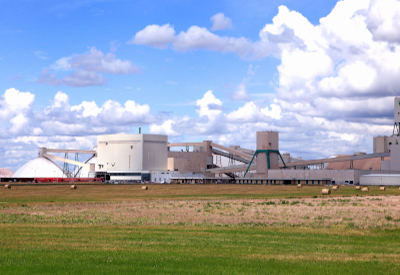
Aug 29, 2019
The United Nations estimates that world population will climb from 7 billion to 9 billion by 2050. This means higher demand for food for the growing population, and more work for the farmers to produce more food. And they will need fertilizers to do it, which is where potash comes in, as 96% of the world’s production of potash is used in fertilizers. The ten potash mines in Saskatchewan presently account for more than 7 million tonnes of potash or about 25% of the annual world production.
The mission of these potash mines is to help the world grow the food it needs. By striving to produce and deliver the highest quality, most innovative crop nutrition products, they help farmers rise to the challenge.
The simplest measure of the health of the potash industry is the price the nutrient commands on the world market. But whether the price per tonne dips to US$150, as was seen in 2005, or skyrockets to US$900 as it did in 2009, the true guarantor of success in the industry depends on cutting unnecessary expenses, ensuring safety and benefiting from the long-term planning made possible by market-leading processes, equipment and technology.
Challenges: Potash is a Beast
Potash is by no means easy to process; demanding material characteristics combined with unique processing requirements make it a challenge to mine. Since potash is a corrosive material, it can progressively destroy metal through chemical action. Potash creeps its way into nooks and crannies to eat into equipment, and hardens into sharp crystals that can cut and tear into seals.
When Scott Paish of Rittal visited some Potash Mines in Saskatchewan, along with Rittal’s distributor partner, Jonathan Petryk of E. B. Horsman & Son, the doors of the traditional Nema 4X enclosures were falling off due to caustic dust lodging inside the hinges causing corrosion. The potash mines were looking for an enclosure to protect valuable automation, instrumentation and electrical equipment that come into contact with potash during processing. Petryk says, “Our main goal has been to find an enclosure that can withstand the corrosive atmosphere, offer all-round protection, and last longer in potash mines. This will help keep the bludgeoning costs in this potash mining industry down.”
Solutions: Hygienic Design is a protector
After evaluating and introducing Rittal’s Hygienic Design (HD) enclosures in two of the potash mines in Saskatchewan, they became more convinced of the solution.
- Smooth stainless steel: HD enclosures are made of high quality stainless steel that resists corrosion, preventing any dirt and debris due to the smooth texture.
- Secure blue seal: The seals around the enclosure doors often fail due to the corrosive potash destroying them. Rittal’s HD enclosures offer the ability to replace just the distinctive blue seal, not the entire door, thus saving huge costs. Furthermore, the one-piece secure air-tight silicone seal does not leave a gap around door for potash to seep through.
- Paish adds, “Usually, the mine workers have to use a screwdriver or sharp tool to chip away the corrosion and build-up around the seals, and often, the enclosure gets damaged. With the HD enclosures, this does not happen, leading to valuable savings in time and costs!”
- Inner hinges: Exposed hinges pose a significant problem, and keep rusting, disintegrating and falling off on all enclosures, no matter who the manufacturer is. Rittal’s HD enclosures are located on the inside of the box. Hence, they are protected against the corrosive dust prevalent in the potash mines.
- Easy mounting: HD enclosures do not have additional holes for mounting which is an advantage, as they are able to mount them any way they choose by welding directly to the enclosure. This enables them to be fitted into any space or orientation, and the absence of holes means less apertures for the harmful potash dust to creep into and destroy!
- Steep sloping roof: The 30˚ roof angle allows liquids to run off easily so the HD enclosures can withstand frequent high pressure wash downs, and the steep slope plus the smooth surfaces prevent bacteria and harmful build-ups on the surfaces.