What Is Corrosion and Why Does VpCI® Help?
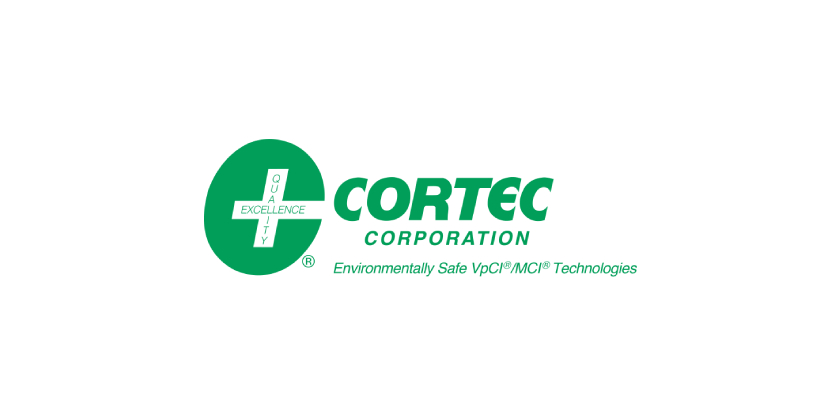
December 2, 2024
Rust is a familiar sight for most of us. Rusty cars, rusty nails, rusty locks, and other forms of corrosion are part of everyday life, causing assets to lose their value and functionality. But while the problem is obvious, the cause and the solution are less apparent to most. However, understanding the cause of corrosion provides an important key to unlocking powerful solutions such as Cortec’s Vapor phase Corrosion Inhibitors (VpCI®) for metals preservation in industrial settings and beyond.
What Is Corrosion?
Corrosion is an electrochemical process that seeks to return refined metals to their natural state. For example, steel is made from iron ore containing iron oxides (aka, a natural form of rust). To turn iron ore into steel, energy (e.g., intense heat) must be added to convert it into a useful state. Unfortunately, as time goes on, there is a strong pull on that refined steel to turn it back into its natural form of iron oxide, or rust.
The Key to Rust Prevention
The key to stopping rust is understanding the corrosion triangle and knowing how to break it. For corrosion to occur, three components typically must be present: metal, oxygen, and an electrolyte. Oxygen combines with metal molecules to create an oxide or corrosion product at what becomes the “anode” site of a corrosion cell. Water provides a perfect environment in which charged particles (electrolytes) can dissolve and electrons can flow from the “anode” to the “cathode” site to complete the electrochemical process. Breaking the connection between any of these elements interrupts the corrosion mechanism and keeps the metal from degrading. If there is no oxygen, the metal cannot oxidize. If there is no electrolyte, it is difficult for electron transfer to take place. If there is no metal, there are no iron molecules to combine with oxygen and create rust.
How VpCI® Breaks the Corrosion Triangle
Cortec’s Vapor phase Corrosion Inhibitors can break two sides of the corrosion triangle by creating a molecular barrier that interrupts the interaction of metal with electrolytes and oxygen. Vapor phase Corrosion Inhibitors such as amine carboxylates have an affinity to metal and can “stick” to them thanks to this attraction. Similar to the effective but temporary bond of a magnet on metal, these Vapor phase Corrosion Inhibitors “adsorb” onto a metal surface, making it more difficult for oxygen and moisture to interact with metal ions. This is like attending a social gathering and finding a table to sit at. If all the seats at a table are already full, it will be much more difficult to engage with the people at that table than if there were an open seat to sit down at. The same is true for metal. If Vapor phase Corrosion Inhibitors are taking all the available “seats” on the surface of the metal, there is no room for oxygen and moisture to sit down at the “table” to have a “conversation” that results in corrosion.
The Vapor-Phase Application Mechanism
While it is important to know how Vapor phase Corrosion Inhibitors interrupt the corrosion process, it is also important to understand how they are applied, since this has direct implications for their benefits and ease of use. A special advantage of Vapor phase Corrosion Inhibitors is that they vaporize or sublimate from a liquid or solid into a vapor, subsequently diffusing into areas of lower concentration until they reach their specific level of saturation. Because these vapors will continue to diffuse through the air unless they are trapped, they must be applied in an enclosed space to keep the protective
layer intact. However, this vapor-phase action makes them much easier to apply to surfaces that are intricate or difficult to reach and eliminates the need to apply greasy rust preventatives that eventually must be cleaned off.
What Does Vapor-Phase Protection Look Like in Real Life?
Sometimes, applying Vapor phase Corrosion Inhibitors is as simple as wrapping an auto part inside a piece of paper coated with Vapor phase Corrosion Inhibitors or putting a component into a VpCI®-126 Blue bag. Other times, it means placing a VpCI®-111 Emitter into an electrical cabinet so Vapor phase Corrosion Inhibitors can diffuse through the breathable membrane, condition the enclosure, and adsorb on intricate metal wires and contacts without disturbing service. Still on other occasions, it may involve fogging waterborne Vapor phase Corrosion Inhibitors into a power plant HRSG (heat recovery steam generator) for preservation during layup with an eye to speedy recommissioning.