Key Factors to Maintaining Arc Flash Safety, Part 1
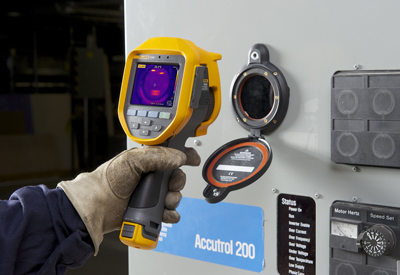
When an arc fault occurs, the result is a massive electrical explosion. The light and heat emitted by the explosion is known as the arc flash, and the pressure wave is known as the arc blast. An arc flash releases hot gases and concentrated radiant energy up to four times the temperature of the sun’s surface, which can melt metal and cause severe radiation burns, damage eyesight, and result in fatalities. The accompanying pressure waves can damage hearing or brain function and send loose equipment, tools, machinery, and debris flying to cause further injuries. Even if an arc blast doesn’t injure a person, it will damage equipment and cause downtime.
Here in Part 1: four of seven arc flash safety measures.
Top causes of arc flash and blast
One of the major causes is voltage transients (spikes) resulting from switching reactive loads or lightning strikes. The transient may last only microseconds, but it may also carry thousands of amps of energy. When such spikes occur while measurements are being made, they can cause a plasma arc to form—inside the measurement tool, or in the air outside. Other major causes of arc flash are things as simple as touching a test probe to the wrong surface, worn connections, gaps in the insulation, improperly installed parts, or dust and corrosion that cause resistance heating.
Top 7 arc flash safety measures
To limit the exposure of workers to the risk of arc flash:
1. Train on safe work practices
2. De-energize equipment before accessing
3. Perform regular preventive maintenance
4. Wear arc-rated personal protective equipment (PPE)
5. Select test tools rated for the environment
6. Use remote display or wireless test tools
7. Install infrared windows for switchgear inspection
The National Fire Protection Association (NFPA) 70E: Standards for Electrical Safety in the Workplace provides the most comprehensive guidance for protecting workers from electric shock and arc flash hazards. The 2015 edition added several new provisions including strengthening electrical safety programs, new test instrument and PPE requirements, expanded training requirements, and redefinition of what constitutes a “Qualified Person” permitted to work in areas where there are exposed energized conductors and circuit components of greater than 50 volts.
1. Train on safe work practices
NFPA specifies that all qualified and unqualified employees persons who work in areas who may be potentially exposed to electrical hazards are present must undergo training to:
• Identify and avoid electrical hazards
• Follow safe work practices such as, proper lockout/tagout procedures, maintaining, hazard boundaries, and abiding by PPE requirements
• Understand emergency procedures
Qualified persons must have additional training on electrical equipment and power systems, to the point where they can demonstrate skills and knowledge of how the system is constructed, its manufacturer recommendations and associated hazards. Qualified persons must also receive training in:
• how to select the correct test instrument, how to inspect it, how to safely use it, what its limitations of use are and interpret the indications
• skills and techniques to test for the presence and absence of voltage
• skills and techniques to determine nominal (phase-to-phase) voltage of the electrical power system
• safe approach distances for electrical shock and arc flash
• perform safety job planning
• assess the risk associated with a specific job task
• select the appropriate methods from a hierarchy of controls, including ppe
• safety-related work practices and procedures to allow them to perform the job task safely
• how to identify and understand the relationship between electrical hazards and injury
2. De-energize equipment before accessing
1. Inspect your test tools and verify them with a known voltage source.
2. Put on the appropriate PPE for the electrical environment.*
3. De-energize and lockout/tagout the equipment.
4. Test for absence of voltage
5. Repeat the meter verification test.
*Until electrical circuits are tested and found absent of voltage, they must be considered energized.
3. Perform regular preventive maintenance
Accidents happen… but some causes of arc flash can be prevented by regularly inspecting electrical distribution equipment. During the inspection, pay specific attention to the early signs of physical failures that are known contributors to arc flash. Repeat the inspection on a regular basis, using a smart phone app such as Fluke Connect® or other portable means to both manage the list of critical components to inspect as well as keep previous/baseline readings field-accessible for the inspection team to compare against. Knowing the health and history of the equipment in your facility is the first step to preventing arc flash. The key to being able to identify an abnormal reading is to gather baseline readings for especially important components and equipment. Critical components for arc flash safety include:
Electrical connections: Use a thermal imager to scan energized components to quickly identify abnormally hot, loose connectors that can signal a variety of potential electrical failures from a safe distance. Make sure to follow all PPE requirements for the full arc flash assessment when opening and closing the door. Follow thermography-specific NFPA 70E PPE guidelines during the infrared inspection, including the distance to maintain from the panel as well as the personal safety gear to use.
Insulation: Test transformer windings, motor windings, and connecting cables with an insulation tester to check the integrity of the cable insulation or motor windings. Low insulation resistance readings may indicate that the cable is breaking down, potentially causing a short. This inspection can prevent premature equipment failure.
Circuit breakers: Proper testing of circuit breakers requires special equipment and specialized expertise. The breakers need to be removed from the circuit and tested to verify the trip current and delay.
4. Wear arc rated PPE within arc flash danger zone
Wearing the proper PPE in conjunction with the other safety measures is critical to minimizing injury in the event of an arc flash incident. In order for the PPE to perform effectively, its arc thermal performance rating must meet—or exceed—the thermal energy transfer during the arc flash incident. The best way to predict the thermal energy transfer, or incident energy, is through an arc flash hazard analysis. Then select PPE clothing and accessories based on performance rating predicted energy exposure NFPA 70E Table 130.7(C)(16).
Personal protective equipment categories
Always abide by the limits of use and minimum working distance. The following PPE categories are described by the National Fire Protection Association (NFPA) Standard 70E. The greater the electrical hazard, the higher the personal protective equipment arc rating must be to withstand an arc-flash incident.
PPE Category 1:
• Panelboards or other equipment rated 240 V ac and below
– Limits of use: Maximum 25 kA available short circuit current and maximum 2 cycle (0.03 sec) fault clearing time
– Minimum working distance: 18 inches (457 mm)
• Storage batteries, dc switchboards, and other dc supply sources
– 100 V dc to 250 V dc, short-circuit current < 4 kA
– 250 V dc to 600 V dc, short-circuit current of 1.5 kA
– Maximum arc duration: 2 seconds
– Minimum working distance: 18 inches (457 mm) Arc-rated clothing, minimum arc rating of 4 cal/cm²
• Arc-rated long-sleeve shirt and pants or arc-rated coverall
• Arc-rated face shield or arc flash suit hood
• Arc-rated jacket, parka, rainwear, or hard hat liner (as needed)
Protective equipment
• Hard hat
• Safety glasses or safety goggles (selection required)
• Hearing protection (ear canal inserts)
• Heavy duty leather gloves
• Leather footwear (as needed)
• No metal-framed eyeglasses, cell phones or radios, jewelry, rings, keys or watches
• Insulated hand tools
PPE Category 2:
• Panelboards or other equipment rated > 240 V ac to 600 V ac
• Other 600 V ac class (277 V through 600 V, nominal) equipment
– Limits of use: Maximum 25 kA available short circuit current and maximum 2 cycle (0.03 sec) fault clearing time
– Minimum working distance: 18 inches (457 mm)
• 600 V ac class motor control centers (MCCs)
– Limits of use: Maximum 65 kA available short circuit current and maximum 2 cycle (0.03 sec) fault clearing time
– Minimum working distance: 18 inches (457 mm)
• Storage batteries, dc switchboards, and other dc supply sources
– 100 V dc to 250 V dc, 4 kA <= short-circuit current < 7 kA
– 250 V dc to 600 V dc, 1.5 kA <= short-circuit current < 3 kA
– Maximum arc duration: 2 seconds
– Minimum working distance: 18 inches (457 mm) Arc-rated clothing, minimum arc rating of 8 cal/cm²
• Arc-rated long-sleeve shirt and pants or arc-rated coverall
• Arc-rated face shield or arc flash suit hood and arc-rated balaclava
• Arc-rated jacket, parka, rainwear, or hard hat liner (as needed)
Protective equipment
• Hard hat
• Safety glasses or safety goggles (selection required)
• Hearing protection (ear canal inserts)
• Heavy duty leather gloves
• Leather footwear
• No metal-framed eyeglasses, cell phones or radios, jewelry, rings, keys or watch
• Insulated hand tools
PPE Category 3:
• Storage batteries, dc switchboards, and other dc supply sources
– 100 V dc to 250 V dc, 7 kA <= short-circuit current < 15 kA
– 250 V dc to 600 V dc, 3 kA <= short-circuit current < 7 kA
– Maximum arc duration: 2 seconds
– Minimum working distance: 18 inches (457 mm) Arc-rated clothing, minimum arc rating of 25 cal/cm²
• Arc-rated long-sleeve shirt (as required)
• Arc-rated pants (as required)
• Arc-rated coverall (as required)
• Arc-rated arc flash suit jacket (as required)
• Arc-rated arc flash suit pants (as required)
• Arc-rated arc flash suit hood
• Arc-rated gloves
• Arc-rated jacket, parka, rainwear, or hard hat liner (as needed)
Protective equipment
• Hard hat
• Safety glasses or safety goggles (selection required)
• Hearing protection (ear canal inserts)
• Leather footwear
• No metal-framed eyeglasses, cell phones or radios, jewelry, rings, keys or watch
• Insulated hand tools
PPE Category 4:
• 600 V class motor control centers (MCCs)
– Limits of use: Maximum 42 kA available short circuit current and maximum 20 cycles (0.33 sec) fault clearing time
– Minimum working distance: 18 inches (457 mm)
• 600 V class switchgear (with power circuit breakers or fused switches) and 600 V class switchboards
– Limits of use: Maximum 35 kA available short circuit current and maximum 30 cycles (0.5 sec) fault clearing time
– Minimum working distance: 18 inches (457 mm)
• NEMA E2 (fused contactor) motor starters, 2.3 kV through 7.2 kV
• Metal-clad switchgear, 1 kV through 15 kV
• Other equipment 1 kV through 15 kV
– Limits of use: Maximum 35 kA available short circuit current and maximum 15 cycles (0.24 sec) fault clearing time
– Minimum working distance: 36 inches (914 mm)
• Storage batteries, dc switchboards, and other dc supply sources
– 250 V dc to 600 V dc, 7 kA <= short-circuit current < 10 kA Arc-rated clothing, minimum arc rating of 40 cal/cm²
• Arc-rated long-sleeve shirt (as required)
• Arc-rated pants (as required)
• Arc-rated coverall (as required)
• Arc-rated arc flash suit jacket (as required)
• Arc-rated arc flash suit pants (as required)
• Arc-rated arc flash suit hood
• Arc-rated gloves
• Arc-rated jacket, parka, rainwear, or hard hat liner (as needed)
Protective equipment
• Hard hat
• Safety glasses or safety goggles (selection required)
• Hearing protection (ear canal inserts)
• Leather footwear
• No metal-framed eyeglasses, cell phones or radios, jewelry, rings, keys or watch
• Insulated hand toolsarc
In Part 2, watch for the remaining three of seven arc flash safety measures:
5. Select test tools rated for the environment
6. Extend your safety zone with non-contact or wireless test tools
7. Install IR windows in panels
Source: Fluke Digital Library @ www.fluke.com/library.