The Practical Benefits of Modular Industrial Enclosures, Part 1
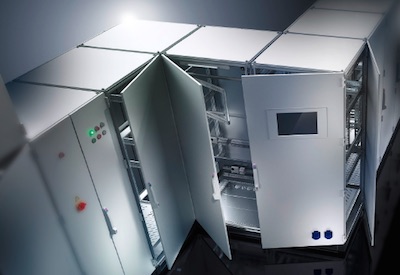
Apr 30, 2017
By Nathan Xavier
Modular freestanding enclosures offer a number of key advantages when compared to traditional unibody enclosures. Many times these attributes are overlooked either out of a false perception of increased enclosure costs, reluctance to change, or a simple lack of awareness of the possible benefits of modular solutions.
This 2-part article seeks to provide a more clear understanding, for designers, integrators and end users alike, of the benefits offered by modular enclosures. Examples will demonstrate the savings that can be realized over the lifespan of an enclosure after factoring in common use and operating costs such as maintenance, modifications and expansions associated with typical industrial applications. Here in Part 1: a comparison of modular and unibody enclosures, and common misperceptions. In Part 2: a comparison of costs.
Definition of modularity
The strength (both literally and figuratively) of a modular enclosure lies with its frame. The frame consists of metal forms with a series of holes spaced at standardized units of dimensions such that common accessories can be added to the interior without drilling or welding. Multiple frames can be joined together (side-to-side, back-to-back, side-to-back, top-to-bottom, etc.) to create infinite configurations. This flexible arrangement is accompanied by an ease of use. Conversely, traditional unibody enclosures are folded sheets of metal with welded seams designed for singular use. Changes are very difficult without costly fabrication techniques.
Common functionality
Although construction methods vary, the most basic functions for either modular or uni¬body enclosures are the same. Both serve as a place to safeguard workers from elec¬trical equipment and safeguard electrical equipment from the environment. Each can be certified to NEMA 250 and UL 50/50E standards to offer the same protection ratings (3R, 12, 4, 4X, etc.). While the main goal of a unibody enclosure ends there, the mod¬ular enclosure strives to provide more. With a modular system the designer, integrator and end user have the freedom to make assemblies as basic or complex as they wish.
Tangible differences
The physical differences between modular and unibody enclosures provide the first dis¬cernible advantages. The most basic differences are described below.
Gasket
The most basic of unibody enclosures use a peel-and-stick strip gasket for the door seal. Most modular enclosures feature a foam-in-place gasket that is poured continu¬ously around the perimeter of the enclosure skin (door, sidewall, and so on) such that no gaps exist. This provides an overall better seal with memory retention. Some unibody enclo¬sure manufacturers have switched to foam-in-place gaskets following the modular enclosure lead.
Hinge/latch
Virtually all unibody enclosures use a piano hinge for their doors. Latching is done with multiple clamps around the door perimeter or a 3-point latching handle. Modular enclosures feature discrete, captive hinging that is hidden from view for greatly improved aes¬thetics. The modular design allows for scalable door latching, which some manufacturers take advantage of by offering 4-point latching.
Paint
Any plain carbon steel enclosure will be required to be painted for corrosion protection. The paint of choice is generally powder paint, known for its hard durable finish. In a closed frame modular enclosure, the addition of an electrophoretic dip-coat primer adds a level of protection beyond that which the unibody enclosure offers. This 2-part primer and powder coat combination ensures maximum corrosion resistance and durability.
Mounting panel
The most commonly modified part on any enclosure, the mounting panel, differs in both construction and ease of use. Unibody panels are generally painted steel and constructed with an L-fold around the perimeter to stiffen them.
Modular panels are generally zinc-plated steel, allowing for an easier, more accessible ground that does not require the scraping of paint. They may also feature a C-fold for easier handling and greater strength.
The modular enclosure design allows for the addition of rails making it possible to slide the panel into and out of the front, side, or rear enclosure openings. This saves time and increases safety when compared to the unibody technique of laying the enclosure on its back and lifting the panel with a crane or forklift.
The construction of a modular enclosure allows for a greater opening and thus a larger mounting panel when compared to a unibody cabinet. Also, because the modular enclosure can be ordered without a cable plinth, the overall size of the unit can be enlarged further increasing the panel size.
External Skins
Modular enclosure skins offer many benefits over their unibody counterparts. The ability to easily remove the door, sidewalls, and other parts allows for greater accessibility and more accurate cutouts and modifications. The inside door surface has a stiffener with multiple holes which is capable of supporting a wide variety of chassis rails or panels, yielding an entire separate mounting surface to be utilized. Standard off-the-shelf uni¬body enclosures only allow the attachment of a print pocket.
Frame
In addition to the aforementioned ability to join enclosures and easily add accessories, the modular enclosure frame will accommodate more door options as well. Custom motor control centre (MCC) solutions can be configured with several smaller partial doors making up the face of the cabinet. Then both horizontal and vertical dividers can be added to the frame, easily separating these compartments (e.g., high/low voltage sections).
Intangible differences
Modular enclosures provide advantages beyond just those physical attributes. These intangible attributes while not as obvious, are just as real.
Aesthetics
No longer is the plant floor a dirty environment where equipment is designed sole¬ly based on function. Modern digital technology has paved the way for a factory floor where cleanliness and aesthetics are nearly as important as ergonomics and reliability. Designers have switched to newer digital control and automation technology. Yet some continue to package their products in enclosures that were designed in the 1950s, resulting in an end product that looks dated like old technology. Modular units, with hidden door hinges and single handle locks versus clamps provide a look more consistent with this newer technology.
Ease of modification
The flexibility provided by a modular enclosure system allows for easier modification. The design process is smoother, with standard solutions available as off-the-shelf accessories. The overall design process is also much more forgiving when using a modular enclosure. Early mistakes can be corrected or late changes can be accommodated much more easily on the modular platform.
Misperceptions
Modular enclosures have gained acceptance in almost every industrial market, however misperceptions continue to exist. Here are the most common of these misperceptions.
Modular enclosures are not as strong as unibody enclosures
False. This misperception stems from the fact that the enclosure walls are thinner in a modular enclosure than a unibody enclosure. However, the strength of a modular enclo¬sure comes from its frame, not the enclosure walls. The load being exerted on the en¬closure due to the weight of the equipment installed is transferred to the vertical frame members. Later we will discuss why the thinner wall material is actually advantageous.
Many part numbers must be ordered to complete a modular enclosure assembly
False. A basic modular enclosure consists of as little as two part numbers: the core frame/assembly (with included mounting panel), and a pair of sidewalls. Coincidentally, the equivalent unibody enclosure will also require two part numbers: the core enclosure plus a mounting panel.
Modular enclosures require a lot of assembly work like an erector set
Assembly work, while required, is minimal for a basic system. The more complex the configuration, the more assembly required, however the system accessories can be added by someone without specialized training, unlike the more difficult fabrication techniques (cutting/welding/bending) needed to modify a unibody enclosure
Modular systems are more expensive
Standard pricing on core systems are comparable to unibody enclosures. Additionally, there are many hidden costs that are reduced when factoring the total lifecycle of the enclosure.
Watch for Part 2 in the June 6 issue of EIN.
Nathan Xavier is a Rittal Corporation Consulting Engineer and has been with the com¬pany since 2007. He holds a Bachelor of Science degree in Mechanical Engineering and provides customer specific applications support relating to Rittal industrial enclosure and power distribution solutions.
The Rittal Corporation is the U.S. subsidiary of Rittal GmbH & Co. KG and manufac¬tures the world’s leading industrial and IT enclosures, racks and accessories, including climate control and power management systems for industrial, data centre, outdoor and hybrid applications; www.rittal.us