Knowing and Selecting the Right Drive Motor
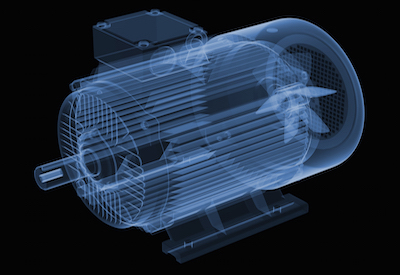
Aug 2, 2018
By Owen Hurst
There are a lot of things to consider before selecting the right motor for your intended use, particularly with recent advancements in drive system technology and control solutions. With a wide variety motor types to choose from, all factors and logistics need to be considered. The days of simply buying a standard electric motor and plugging it into your application are gone.
With the global push for efficiency, using motors that consume a large amount of energy and run at full speed for prolonged periods of time has been replaced with a plethora of more efficient options. But before considering the necessary concerns regarding motor purchases we need to briefly step back and look at the history of motor development and why the options for drive motors and controls has become such an essential component.
A brief history
It has been over 180 years since the introduction of the first electric drive motor, and since then there has been a steady progression in solutions related to the transfer of motion and the numerous types of electrical machines in operation.[1] Moving forward to more recent times there have been periods of popularity for particular motor types that helped to drive the industry to better the available solutions. DC drives, which had a peak in popularity in the 1990s, are now typically used in specialized industry sectors (although the ongoing AC vs. DC debate and expansion of products requiring DC power may lead to a resurgence).
Even more recently than the DC drive peak has been the focused use of induction motors, driven by their simple construction, reliability, low cost and control applications. Globally more than 90% of users have reported using induction motors in their industrial systems.
However, the energy required to power these motors is a growing issue. Electrical motors consume roughly 30-40% of global power output, and about 90% of the power used by the industrial sector.[2]
In a world increasingly focused on limiting energy consumption through technological advancements, drive motors have become a key focus to lower global energy consumption rates. The problem received regulatory attention in Europe, where the EU banned the sale of the lowest efficiency electric motors in mid 2011. For a listing of IEC efficiency standards for electric motors, visit http://www.iec.ch/perspectives/government/sectors/electric_motors.htm
The answer to lowering the consumption rates of drive motors has come in the form of more efficient drive motors and advanced control solutions with real-time energy monitoring and varying the frequency or speed of drives. One of the most talked about is the rise of variable frequency drives (VFDs), also known as variable voltage frequency drives (VVDFs), variable speed drives, micro drives, or inverter drives. Essentially, a VFD is an adjustable speed drive system that controls the speed and torque of an AC motor by adjusting the motor input frequency and voltage. Additional motor types making their way to the playing field are permanent magnet synchronous motors (PMSM), as well as rising interest in the use of stepper motors and brushless direct current motors (BLDCM).
Choosing a suitable motor
with a variety of options for motors and motor control systems now available, the question becomes which motor to choose for your application? And admittedly, it is not the easiest answer at first glance, but requires a variety of considerations.
Start by asking yourself these questions:
1) What is the maximum speed I need for my application?
2) How much torque do I need?
3) Are there size restrictions I should be aware of?
4) Environmental conditions in the application location? (e.g., dust, direct heat, moisture, air flow…)
5) Do you plan to use a control system?
6) What’s my budget?
These are the primary considerations before selecting a drive motor, and will lead you to the next big question. Do you choose an AC or DC motor? And to answer this question we need to briefly consider the primary differences.
DC motors typically have a high spin rate (more than 15,000 rpms) that must be adjusted to your use but can operate off batteries. These motors are found a variety of applications, from small items to industrial machines. The motors are small, have relatively simple control systems, can start and stop quickly, and are relatively cost effective. However, they are not exactly precise (speed fluctuation is possible), and are susceptible to degradation from environmental impacts or excessive loads.
AC motors cannot be powered using batteries and require direct power connection. But like DC drive motors, they have a wide application range from household items to industrial applications. They also tend to be lighter, produce less friction, have a longer lifespan, higher starting torque, lower maintenance costs, and for synchronous AC motors no slip. However, they are harder to control in terms of speed, communication systems are more intensive and complicated, they tend to be rather noisy, and in terms of induction AC motors they require a starting switch and can experience rotational slips.
After considering the preliminary questions regarding your application requirements and briefly outlining the primary advantages and disadvantages of AC and DC motors, purchasers are better positioned to choose the motor that will be most cost effective for their application and provide the highest ROI in terms of energy consumption, product life and functionality.
Owen Hurst is Managing Editor of EIN’s sister publication, Panel Builder & Systems Integrator: http://panelbuildersystemsintegrator.ca
Notes
1. Teresa Orlowska-Kowalska, Mateusz Dybrowski. “Industrial Drive Systems. Current State and Development Trends,” Power Electronics and Drives 1 (36), 2016. p. 5
2. Otto Herman., Design Principles for Industrie 4.0 Scenarios, 2015; K Schwab, The Fourth Industrial Revolution, 2016