3 Steps to a Strong Safety Program
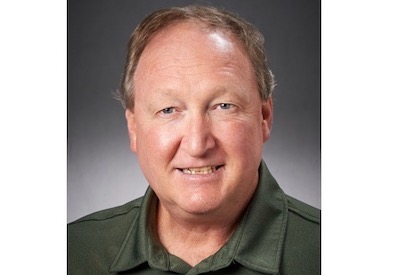
May 13, 2020
By Sean Silvey
More than 70% of workers believe there is an opportunity for more electrical safety training in the workplace, according to a January 2020 Fluke survey of 162 electrical workers. Three reasons why electricians may feel they don’t get enough safety training for their jobs are because effective programs take a lot of time to set up, employees are often not engaged in the training or safety meeting, and safety isn’t talked about in a way that builds toward a strong safety program. Here’s what you can do to create a stronger training program.
1. Setting up or building a training program
Creating a new safety training program or building onto an existing program can take some time but can also help create a strong culture of safety as it becomes more engrained in the employees’ daily thoughts and actions. Michael Brooks, a project coordinator at Great Southwestern Fire and Safety (GSF) believes training has made all the difference with his employees. “I think one of the things that has been helpful is our insistence to work one-on-one with as many people as possible and help them learn and then grow and do the right thing. Help them get better trained.”
Brooks went on to explain that the success GSF has seen with workers staying safe is also due to how that one-on-one training continues down the line. The more experienced workers at GSF take the time to teach newer employees, and over time those newer employees become the trainers. “Once they’ve learned, they’ve been able to translate that to somebody new. It’s not the same people teaching and learning, but we’re growing all the time.”
Safety culture expert at Predictive Solutions, Chuck Pettinger, Ph.D., has seen a lot of successful and unsuccessful training programs over the years. He says one of the hallmarks of a good safety training program is making it personal. Teaching one-on-one is a great way to accomplish this. Dr. Pettinger has also seen training programs work well when the teacher adapts their teaching styles to the class’ or individual’s learning styles.
2. Get workers engaged in safety
No matter what approach you take, Dr. Pettinger suggests taking steps to ensure everyone is engaged in the training. And that often leads to a safer workplace. “In my studies, culture and engagement truly are part of world-class organizations.”
Getting employees actively engaged in training programs and safety meetings can be difficult. Dr. Pettinger has seen success around a few incentive programs. One example he gave was based on employees earning points for participating or presenting during training and safety meetings. These points could then be saved up for a gift card or donations to a local charity. Setting up short-term initiatives like this helps get employees more involved. Over time, these actions help engagement and became a part of our workers’ everyday lives, and can potentially improve the company’s culture.
Another way to get employees actively engaged is by using “planned” spontaneous recognition. Dr. Pettinger suggests planning an event or reward around a positive milestone; for example, getting coffee for everyone when the group has hit one thousand safety observations. This can get workers excited about their job and keep safety achievement oriented.
Dr. Pettinger also warns against counting how many days since an injury or accident. Instead of getting workers to think about safety, this often drives them to just not report injuries so that they don’t break the streak. Instead, try focusing on tracking the quality of the safety inspections, or how many employees participate in a safety initiative. In general, people are more motivated when they are trying to improve something, rather than trying to avoid or reduce something (e.g., injury rates).
3. Communication is key
How we talk about safety can make or break a strong culture of safety. Dr. Pettinger suggests trying to coach employees instead of policing them. Focusing on the negative side of safety, like using visual injury tracking mechanisms like a stop sign, can end up eroding any progress made toward a strong culture of safety.
Instead, talk about potential injuries or near misses regularly and use these as teachable moments. Dr. Pettinger said he’s seen success in “randomly observing what [employees are] doing and providing feedback when we see somebody drift. ‘I noticed that when you’re working, your hand is getting really close to that pinch point. I sure don’t want to see you get hurt. Let’s make sure we watch out for each other.’ And that little thing may be enough to refocus and reduce that chance of an injury.”
Communicating when a worker is at risk of injury, using the moment as an opportunity to walk through the safest steps, helps create a culture where employees feel more comfortable asking questions and learning. It makes the safety training more personal, takes it out of the formal setting, and helps workers continually learn and refocus on safety.
Sean Silvey is a product and application specialist for Fluke, which manufactures electrical test and measurement tools, including multimeters, clamp meters and insulation, earth ground and installation testers.
Getting geared up in proper PPE can take time but should be seen as a necessary step to keep workers safe.
If you notice a worker putting themselves at risk, use the moment to coach and teach the employee how to stay safe so they will take the proper steps in the future.