The Practical Benefits of Modular Industrial Enclosures, Part 2
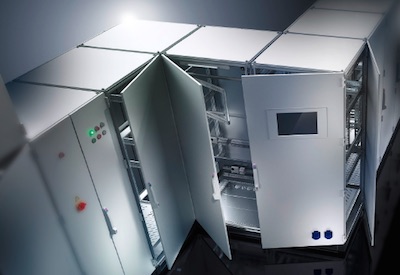
May 7, 2017
By Nathan Xavier
Modular freestanding enclosures offer a number of key advantages when compared to traditional unibody enclosures. Many times these attributes are overlooked either out of a false perception of increased enclosure costs, reluctance to change, or a simple lack of awareness of the possible benefits of modular solutions.
Part 1 of this 2-part article explored the similarities and differences between modular and unibody enclosures. Here in Part 2: a comparison of costs.
True cost
Most people are familiar with the concept of ROI (return on investment). Considering the savings or possible yields of a decision beyond the initial cost is a wise course of action in any business. For the purposes of this paper, a variation of this concept will be employed which will be referred to as “true cost.” True cost is calculated by simply totalling the costs of an enclosure solution over the course of its lifecycle via practical examples, and is represented by the short equation below.
Acquisition costs + use costs + operating costs = true cost
Acquisition costs are realities for control panel shops, integrators, OEMs, and end users alike as these costs are passed down from one group to the next. However, when taking the actual design and procurement processes into account, the primary benefactor of reduced acquisition costs will be the system designer. However, after the initial purchase decision is made, panel shops and integrators are more likely to be concerned with use costs while a significant portion of the true cost for end users will come from operating costs. Use costs are mostly attributed to labour and the use of floor space during integra¬tion, while operating costs generally include labour for maintenance, lost productivity due to downtime and costs incurred during expansion. The inherent advantages of modular enclosures can substantially reduce all of these costs.
Acquisition costs — primary design and physical acquisition
When considering the acquisition cost of enclosures or enclosure systems, all phases of design as well as the procurement process should be considered. After all, the easier an en¬closure system can be configured and sourced, the cheaper its acquisition cost will become.
With a traditional unibody enclosure, system designers must be careful to accurately define the scope of work of a project such that this information can be conveyed to an enclosure manufacturer. The enclosure manufacturer then must determine if the scope of work will fit within its manufacturing processes. If the scope of work isn’t well defined, assumptions will need to be made and dialogue will begin regarding the design. Even if the scope is fully understood, odds are high the enclosure manufacturer will need to ask the designer to make concessions based on their capabilities. The potential for a lengthy RFQ-to-redesign-to-quote-to-redesign-to-requote loop is probable. If successful, the end result is likely a special¬ized configuration with a very long lead time.
Modular enclosures enable the designer to create special one-off configurations using standard catalogue items. Compatible solutions are pre-engineered such that direct communication with the enclosure manufacturer may not be necessary. There is a much greater probability of these standard parts being in stock, significantly reducing lead times.
Use costs
Use costs at integration and panel shops, time and floor space are always at a premium. The more labour needed to perform and complete a task, and the more space it re¬quires, the less efficient the processes of the entire business become. This translates to lower productivity and, as a result, less profitability.
Use cost — door removal
Human machine interface components require modifications to be made to the doors of industrial control enclosures. Traditional unibody cabinets use a continuous (piano) hinge for the door. Removal and installation of a door with this type of hinge can take up to 30 minutes. For this reason, most integrators choose to leave the door in place and perform cutouts while the enclosure is on its back—taking up valuable floor space and in many cas¬es, incurring additional labour costs involved in tilting the enclosure on its back including the possible use of cranes or forklifts. When cutouts are done this way, it is very common for the metal shavings created by the cutout to fall into the enclosure — requiring a thorough clean¬ing to remove and adding even more labour costs to the process.
Conversely, the doors of a modular enclosure are attached by multi-point, captive hinges and can be removed in as little as 30 seconds and taken to a separate location for modifica¬tion. The costs associated with properly positioning a unibody enclosure for door modifica¬tions are completely eliminated and as an added benefit, work can be performed inside the enclosure at the same time as the cutouts are being made to the door resulting in increased productivity.
Use cost — adding cutouts
The time and cost benefits of performing cutouts at a separate location do not end with the door. With a truly modular enclosure, all of the skins including the sidewalls and roof are removable as well. Since it is very common for enclosures to be modified to accommodate, among other things, some type of component cooling solution such as fans, heat exchang¬ers or air conditioners, the ability to simply remove the mounting surface for modification is a tremendous advantage. As with the door, performing cutouts on the other surfaces of unibody cabinets uses valuable floor space, requires cleaning and often, additional time and labour to stage the enclosure with forklifts or cranes.
Beyond the logistical and labour benefits that modular enclosures provide when adding cutouts, the maintenance and purchase cost of tools used to create the cutouts benefit as well. Unlike unibody cabinets, the strength of modular enclosures comes from the frame and not the skins. This difference is beneficial because, with average steel thicknesses of 10-12 gauge for unibody and 14-16 gauge for modular enclosures, performing cutouts to the skins of modular enclosure is easier on the tools used to make them — increasing tool life and thereby decreasing tool maintenance and replacement costs.
Use cost — mounting panel removal and replacement
Mounting panel removal and replacement in a unibody cabinet can require extensive labour and machine costs. A crane or forklift is needed to put the enclosure on its back, remove the panel for equipment installation, drop it back in over the studs and then raise the enclosure back to its upright position. In the case that multiple enclosures and panels are needed for a project, the enclosures must be staged due to limited crane availability, monopolizing valuable floor space that could be used for other jobs. With the additional movement of the enclosure and occasional unpredictability that comes with using a crane, there is a greater likelihood that the paint finish on the unibody enclosure will be damaged.
Mounting panels customarily found in modular enclosures are larger in height and width, depth adjustable, and easily slide in and out of the enclosure. In addition to the benefit of easily adjusting the mounting panel depth, use cost savings include the labour to install panels (panels slide in and out) without the need for staging and craning, and the elimi¬nation of additional required floor space.
Use cost — weight
Because of their thick 10-12 gauge steel construction, unibody cabinets weigh consid¬erably more than their modular counterparts. Without sacrificing strength or protection, modular enclosures are lighter and thus easier to transport around the shop floor and cheaper to ship, resulting in significant savings of time and freight. Typically, weight savings for modular enclosures are 75-175 lb for single door and 300 lb for double door configurations when compared to unibody equivalents.
Use cost — special configurations
Last minute changes and/or re-designs can often happen. Modular enclosures offer the ability to reverse the door hinge, replace a rear wall with a door, swing a side panel, or add an accessory with little more than a few self-tapping screws. Unibody options are limited to expensive fabrication procedures and may not even be possible to implement in the field, leaving a special order from the enclosure manufacturer as the sole option.
Operating costs
End users can benefit from use costs as well. However, it is easier to demonstrate the benefits of using modular enclosures when viewed from the perspective of saved oper¬ating costs. Savings include labour for maintenance, more productivity due to decreased downtime, and easier expansion capabilities.
Operating cost — maintenance
Scheduled maintenance on machines and control panels is necessary to keep opera¬tions running smoothly. Unscheduled maintenance, on the other hand, can cost a com¬pany millions of dollars in lost productivity. The flexibility of modular enclosures makes them easier to maintain and limits users’ exposure to unplanned downtime. Doors, walls and roofs can all be removed within minutes of an occurrence allowing for easier access to installed equipment and simplifying what can be very labour intensive processes with unibody enclosures — even under planned conditions. And since mounting panels easily slide out of the front of modular enclosures, the panel can be removed without time-con¬suming enclosure staging In the event that an accident damages a modular enclosure; often times, the affected enclosure surface (sidewall, door(s) or roof) can simply be replaced. Unibody cabinets do not provide this flexibility. At a minimum, all of the com¬ponents will need to be removed from the cabinet and repairs made by cutting out the damaged surface(s) and welding new sheet metal in its (their) place. If enough damage has occurred, the entire cabinet may need to be scrapped.
Operating cost — expansion
A factory floor is a dynamic environment where needs can frequently change. If the control panel in a unibody cabinet is full and additional equipment needs to be installed, a new, larger enclosure is usually required. With this comes the removal and reinstal¬lation of existing components to the new panel. Conversely, if a similar need to expand the capacity of a control panel arises while using a modular enclosure, multiple options exist to quickly and easily install new equipment to complete the expansion. Solutions include installing partial mounting panels, chassis bars, or 19” rails. These options are standard accessories for most modular enclosures that seamlessly integrate into the existing cabinet.
In the event that an expansion plan exceeds the size of the existing enclosure but requires that the added equipment be housed with the previous components, the difference between modular and unibody enclosures is also clear. Using a unibody cabinet under these circumstances, as in the previous panel example, requires a completely new and larger enclosure populated with both the new equipment and the existing components that have been removed from the prior cabinet. In this same situation, using a modular enclosure solution, it is possible to expand the original enclosure by simply joining another enclosure to it. Because all of the walls of modular enclosures can be quickly removed, enclosures can easily be joined together in nearly infinite configurations to accommodate expansion — front-to-back, side-to-side and so on. This flexibility saves time, money and frustration because it allows end users to adapt their current installations to suit new needs instead of starting over from scratch as required with unibody cabinets. Modular bayed suites can grow to be as large as needed over time or even scaled back if necessary, offering levels of convenience and customization not available with unibody cabinets.
Conclusions
Despite a number of functional and financial advantages offered by modular enclosures as compared to unibody cabinets, portions of the industry continue to adopt a somewhat shortsighted focus based solely on acquisition cost, and in some cases, the mistaken notion that modular enclosures are inherently more expensive. When specifications for control panels and other applications are written, the true costs and benefits of using one enclosure solution over another must be fully considered, especially in today’s economic climate where every penny counts.
While in some cases choosing a unibody cabinet might seem to be a more cost-effective course of action at first glance, once the use and operating costs are factored into the equation, a unibody solution may prove to be cost-prohibitive. Because the lifecycle of a typical industrial enclosure is filled with planned and unplanned changes and/or repairs, using a modular platform can limit exposure to risks associated with additional costs and downtime, often making a modular enclosure the most sensible choice. Modular enclosures provide the protection required for industrial drives, controls and other equip¬ment along with the practical flexibility to evolve with the changing demands of modern business, all while saving time and money over the course of their lifecycles.
Nathan Xavier is a Rittal Corporation Consulting Engineer and has been with the com¬pany since 2007. He holds a Bachelor of Science degree in Mechanical Engineering and provides customer specific applications support relating to Rittal industrial enclosure and power distribution solutions.
The Rittal Corporation is the U.S. subsidiary of Rittal GmbH & Co. KG and manufac¬tures the world’s leading industrial and IT enclosures, racks and accessories, including climate control and power management systems for industrial, data center, outdoor and hybrid applications; www.rittal.us