Chad Alexander on Contact Automation and System Integration in Oil & Gas
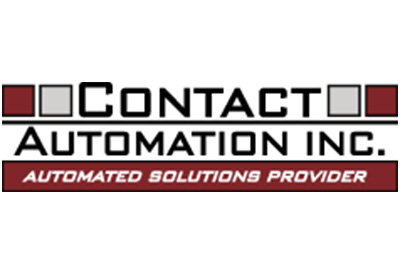
Dec 2, 2019
By Blake Marchand
Chad Alexander is a Branch Manager with Contact Automation, which provides automation integration and control services for the Oil & Gas industry throughout Western Canada and Northwestern United States. Their services include: Consultation and Integration of Automated Control Systems, Panel Development and Fabrication, SCADA System Design and Maintenance, HMI Development, Electronic Product Innovation, and Site Commissioning with Start-up Assistance.
In the interview below Mr. Alexander provides his perspective on the industry, while discussing his career, technology in the Oil & Gas industry, and some interesting projects for Contact Automation.
With respect to the latter, Contact Automation is looking to reduce costs and improve functionality for their clients by upgrading outdated systems.
As Chad mentions below, Contact Automation primarily operates in the Oil & Gas industry, while also doing work in Manufacturing, Food, and Municipal Water & Wastewater. They recently upgraded a SCADA solution using Ignition SCADA to optimize the water and wastewater system for Sylvan Lake by implementing a MQTT protocol.
“Sylvan’s SCADA network was originally designed as a serial radio network. With legacy equipment almost 20 years old and numerous configurations, the system was inflexible and didn’t allow users to communicate reliably with remote stations,” Systems Integrator and PLC programmer, Crayton White explained in the project case study.
“In a nutshell, the town no longer trusted the communications system in place to monitor and manage their critical utility infrastructure,” explained White. “The growing number of system-wide errors, manual processes and old technology was hampering their goal of achieving a fully automated solution.” Sylvan was running a system that had begun to show its age, particularly with added stress caused by the town’s elevation. As a result, it was becoming increasingly costly to do field maintenance on all of their assets.
“Sylvan Lake can now trust that the system they use to manage their water operations and the data it generates is reliable,” said White. “They can communicate with their entire team from a central location, have reduced the points of failure and eliminated the need to physically drive from station to station to check and monitor their infrastructure multiple times a day. The communications reliability of field radios is nearly 100 percent.”
Chad noted that they are trying to implement MQTT systems in the Oil & Gas industry to a similar effect as with Sylvan Lake’s water treatment systems.
“Adding MQTT at the edge makes the field stations smarter, while keeping the system’s overall footprint and bandwidth requirements small,” said White.
The simplicity of the technology makes it an economically viable upgrade option that also improves performance and maintenance.
“Typically, the more hardware you put in, the costs to purchase and maintain the system go up. FreeWave and Ignition gave us the ability to migrate and upgrade each station to achieve IoT at the edge by simply replacing the radio hardware.”
Chad noted they often run into 20-year old outdated systems that are quickly becoming sub-optimal. Particularly, with the uncertain economic landscape of Western Canada’s Oil & Gas industry, implementing more efficient, higher functioning systems can allow their clients to reduce costs and be more competitive.
Can you tell me a bit about your career thus far, what has led you to your current position; perhaps touching on what got you interested in pursuing a career in automation?
I received a diploma in Electronics Engineering from SAIT (South Alberta Institute of Technology). Upon graduation I got into the Instrumentation field and worked towards an Instrumentation Journeyman ticket. I worked for a number of years for Petro-Canada where I started working towards an Electrical Journeyman ticket. I then went back to the contractor services field doing Instrumentation/Electrical and programming work on Gas Compressors.
I moved to Contact Automation in 2010 and started programming full time. My interest in PLC programming came when I was an Instrumentation Apprentice in the late 90’s. A variety of factors (primarily picking up a second Journeyman certificate) led me away from my end goal of programming. At this point in time, I would not go back to the tools. I enjoy my career as it brings numerous challenges and it is always keeping me engaged.
What is your day-to-day like as a Branch Manager for Contact Automation? What challenges you, what interests you, how does it differ from your previous roles?
Scheduling work and coordinating with clients is the biggest challenge. This is due to co-ordination requirements with other trades and other scheduled work. In our industry, deadlines and schedules are tight and often times this causes conflicting schedules.
Personally, I am interested in automation because of the challenge the work brings. It is constantly changing and constantly evolving, which creates a dynamic that I am driven towards. I cannot do a job that is repetitive and boring; I found over my career that I needed to be engaged and challenged to be happy.
My previous experience in the Instrumentation/Electrical field found that over time the tasks become very repetitive and led to boredom. With the automation field, a programmer is constantly improving their logic and making enhancements to improve the final product. If a programmer is bored, then they are not evolving with technology or self-improvement.
Are there any projects you have worked on that have been particularly fascinating for you?
The largest facility I have completed to date evolved over a 4-year time span. This project has created a pretty good sense of pride. I have received a lot of compliments on the HMI and how user friendly it is for operations to run the facility from.
The project that is fascinating is the current project that I am on. Which is making synthetic diesel fuel very economically when compared to conventional methods. It is very challenging and has great future prospects for Canada, USA and worldwide.
With respect to industry trends or technologies, what is interesting to you right now/what’s pertinent to what Contact Automation does?
Our industry (Oil and Gas in Western Canada) lags technology by a number of years. This is primarily due to reliability and economics. We have been involved in some experiments to reduce cost and make improvements to efficiency. However, the majority of our projects continue to be implemented with wiring methods and technology that is 20 years old.
My co-worker has been heavily involved with developing SCADA Ignition software MQTT protocol integration into a FreeWave radio. There is a white paper written about the project. We are actively looking to incorporate MQTT into future projects as we see a large benefit to utilizing the protocol.
Building off the previous question, is there anything you see as becoming more prominent 5-10 years down the road? Particularly with respect to what Contact Automation does.
Definitely the MQTT protocol with respect to SCADA integration. It would be beneficial in a large plant facility where some Maintenance Management software was incorporated into the automation control system. I personally see the future becoming more connected into the Automation Control systems. Think industrial IoT.
Can you tell me a bit about Contact Automation? What industries/industry sectors take up the majority of your work?
We are primarily serving the Oil and Gas Industry. A smaller section of the market for us is the manufacturing, food, water/wastewater and refining industries.
What is an ideal project for you?
My personal preference is the larger projects or projects that utilize more technology.
What are the keys to your success as Branch Manager and, ultimately, the success of Contact Automation?
Maintaining customer service. As an Automation contract services company, we are open 24 hours a day and 7 days a week, which is not typical for Automation companies. I personally take great pride in the work I do. With jobs that we are tasked with designing the automation system; I treat them as though we are the ones who own the asset and ensure the automation system is appropriate from a logistics and economics perspective.