How to Properly Approach and Complete a Migration or Automation Upgrade in Your Facility
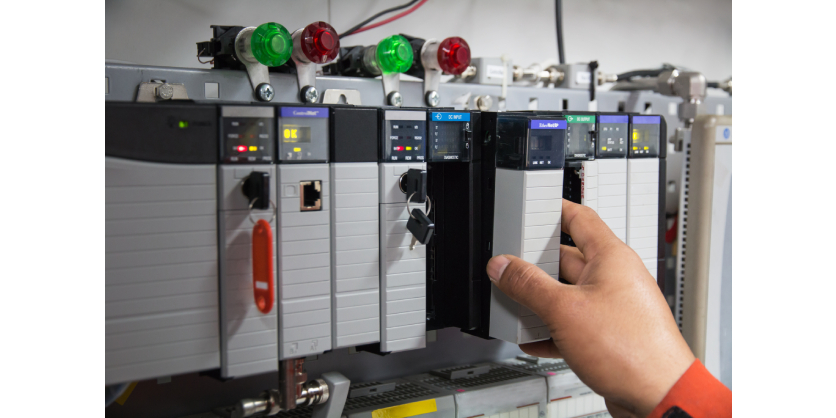
January 2, 2024
By Krystie Johnston
Rexel Canada Electrical Inc. is a global electrical distribution organization known in Canada under brands like Nedco, and Rexel Atlantic. Rexel is a leading distributor of high-quality electrical products and services for the residential, industrial, and commercial markets and they have a variety of specialists located across the country to assist customers with their needs. In this article, Randy Hayward, C.E.T., Manager – Industrial Automation Division Rexel Canada Electrical Inc. Atlantic Division, and Sébastien Larouche, Advisor in Automation and Motor Controls, Nedco Quebec discuss how to properly approach and complete a migration or automation upgrade.
Mr. Hayward has been with Rexel for about five years and brings over 3 decades of experience to the position. He has previously worked with Schneider Electric, Rockwell Automation and Graybar Canada. Mr. Larouche has been with Nedco for 11 years and has more than 25 years of experience working in the automation industry.
Migration vs. Upgrade
While the terms may be used synonymously, there is a difference between a migration and an upgrade. A migration is essentially a direct translation of an existing control system onto a new one and, ideally, keeps as much of the same equipment as possible. An upgrade is the introduction of new features to improve the efficiency, productivity, or safety of the existing system, for example.
The complexity of each is a differentiating factor. Larouche says, “Usually, a migration is a big project. They need to plan the shutdown of the mill or site. Whereas with an upgrade, it could be done in an hour,” depending on the complexity of the project. “A migration means they already have the installed base; they have old equipment that is usually obsolete and is no longer supported by the manufacturer. An update may only be new versions of software, an upgraded CPU, or firmware for the PLCs or HMI.”
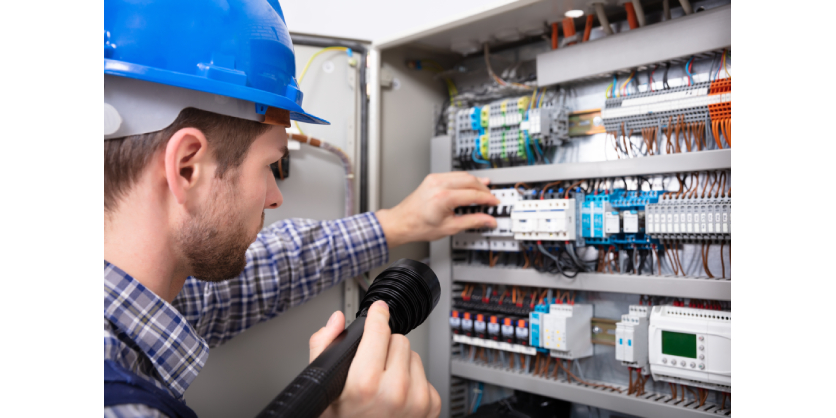
There are many reasons why a company does a migration or upgrade. Although there are often similarities, it usually is a case-by-case scenario because it depends on what they are trying to achieve and their goals. “Usually, it is because the platform that they currently have will not do what they want it to do now – it is just too old, or not powerful enough, not expandable, or able to link to their other systems. Or they can no longer get spare parts and are experiencing premature failures and production issues,” says Hayward.
Planning a migration or upgrade with lifecycle management
When a company decides to do a migration or upgrade, there is no one-size-fits-all solution. But there is a best practice approach that will help make the process go smoother, and that involves an appreciation of lifecycle management. Lifecycle management leverages the capacity of the existing automation investment while at the same time simplifies integration of new generations of technology. With an estimated $65 billion in automation assets approaching the end of their useful life cycle, it is important to have a plan in place to assist with their replacement1.
“Lifecycle management is not just designing, purchasing and building [an automation asset], it is maintaining it and making sure that you can update it and future-proof it as much as you can, and plan for obsolescence. And when that obsolescence comes, what is the next step? Sometimes you throw the whole machine out and start from scratch. But that is not usually how our customers work. Usually, they will say, ‘Look, I want this machine to do this now. Can you help me get there?’”
Randy Hayward, C.E.T., Manager – Industrial Automation Division Rexel Canada Electrical Inc. Atlantic Division
It is always best to plan a migration or upgrade with plenty of time to spare. Hayward says, “Anything under six months is generally an emergency, a rush, and not ideal. I would say you should start that discussion two years in advance. And that discussion is new hardware, new software, who is doing the engineering, who is doing the programming, who is going to lay out the systems, how much downtime will it take to do it, what pieces of equipment can we do – can we do it in stages or does it have to be done all at once?”
“All this needs to be laid out, and the more planning and work completed up front means a smoother implementation. However, we do not always have that luxury and we often get calls about replacing an old PLC or HMI with something new because the machine is down and we cannot get spares”
He adds, “If I could pick an ideal time, you should start your migration and your upgrades five years in advance. Why five years? Because the way businesses work with capital expenditure involves getting the money, planning the machine, planning the downtime, planning the maintenance. It could be two years before it even gets budget approval.”
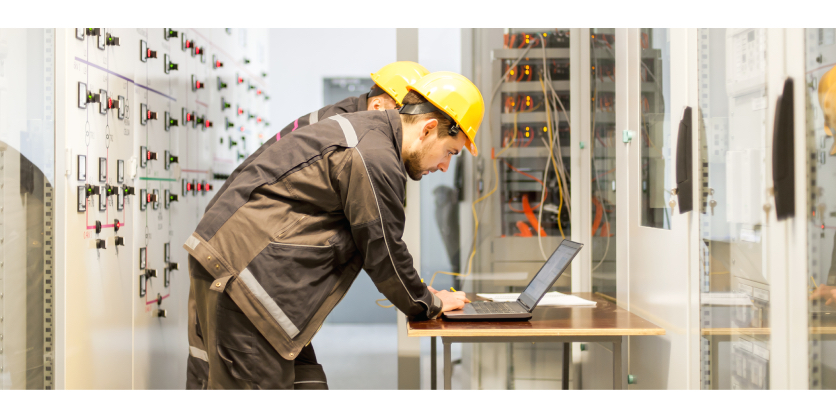
The life expectancy of any automation asset plays an important role in this cycle. Regardless of how well-designed or maintained an automation asset is, at some point, all or part of it will need to be replaced. When it comes time to do the migration or upgrade, Nedco can help. Laroche says that being prepared is important. “The customer, the integrator, and the engineering firm needs to be certain that when they push the button, the mill is going to run again.” Yes, a migration or an upgrade can be done in one step, but usually it happens in several stages, and there are several advantages to this approach.
Laroche says, “Usually, a customer does a migration in two or three steps, to make sure that it is done correctly and that everything will work as planned. For example, one step might be in one area of the mill; the integrators do one section, and check it, and when that is done, they do another, and check it before doing the final section. If they do all the steps of an upgrade at the same time, it usually takes more time, it takes more people, and there is more pressure because you need to be sure that the mill is going to start up again.”
Putting the customer first
Regardless of whether the migration or upgrade happens in stages or is a complete rip and replace, Nedco approaches the project the same way. They start with the customer and what their needs are. Larouche says,
“When I go to the mills or see a customer, the first thing I do is take note of where the critical areas are, and where the process is most likely to experience a bottleneck. What I look for are the sections that, if they go down, will cause the entire mill to go down. That is going to be the priority of the migration. This section needs to be done first to make sure that you can maintain the mill and keep the process running.” He adds, “After that, when you change the hardware, you can keep the old parts as spares for the other PLCs, and then they can move on and make the next change.”
Sébastien Larouche, Advisor in Automation and Motor Controls, Nedco Quebec
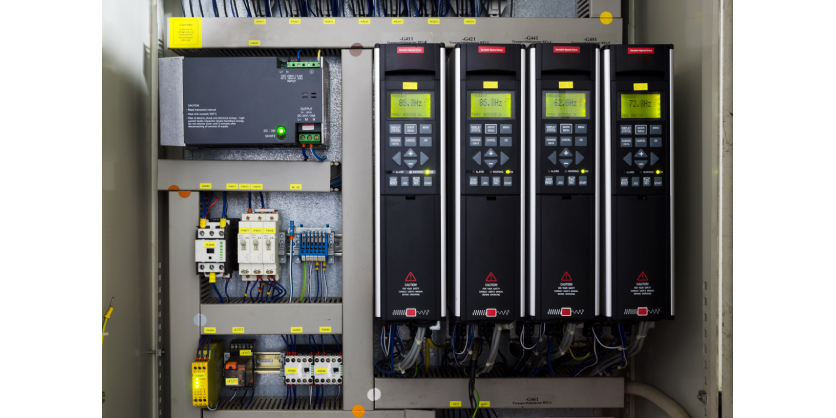
Nedco/Rexel’s approach to properly planning and completing a migration or upgrade always starts with the customer. The customer knows their plant, their long-term strategy, and they understand their restrictions for downtime. They know what they can and cannot absorb at one time. Hayward says that the first meeting is always about learning what the customer needs. He will ask them, “Where are you going to be in three to five years?” Often, what comes out of that surprises the customer because Nedco/Rexel experts can provide insights that they might not be aware of.
“We sit down and come up with the game plan and the long-term strategy about how you are going to get there. Which pieces are most critical, which pieces have to work, which pieces would be nice to add if the money in the budget is there? Often, a customer will discover that they can enhance the productivity of the overall process with new technology which adds features and benefits that wasn’t even conceived of when the machine was first designed and built. This is where we come in because we know the hardware, the software, and its capabilities and it is critical to have a team like Sébastien’s involved in that discussion.”
Randy Hayward, C.E.T., Manager – Industrial Automation Division Rexel Canada Electrical Inc. Atlantic Division
Nedco/Rexel are the bridges that connect what the customer wants to do to what the possibilities are to achieve it. When it is time to do a migration or upgrade, many companies do not have an expert on site who can do the job. Nedco/Rexel can recommend a systems integrator who is experienced in their industry, which is a tremendous benefit. Most system integrators can learn about a product with support from the technical team, what is more difficult to learn are the processes of specific industries.
Laroche says, “We have systems integrators that are specialized in the mining industry, for example, and other systems integrators that are specialized in the food and beverage industry. We have system integrators that we can recommend to our customers. To do a migration, you need to have the right people who understand your business and processes with experienced people on board.”
A partner you can trust
Choosing a good partner is important – especially when automation assets need to be replaced. Hayward offers some practical advice based on his experience in the automation industry. “Pick a supplier that (1) has been in business long enough to have the expertise to support them, (2) has the distribution chain locally that will support them, and (3) has equipment that is familiar enough to the general engineering population. Add a competent systems integrator or engineering firm to that list and you are going to be successful.”
“Do not buy automation gear based on price alone. There is always going to be somebody who has something cheaper, and that is always the most expensive solution. Buy your equipment based on openness and connectivity and long term viability. I have had customers tell me, ‘If you do not do Industrial ENET (open protocol), we are not doing business with you because we are not going to be locked into a proprietary network anymore.’”
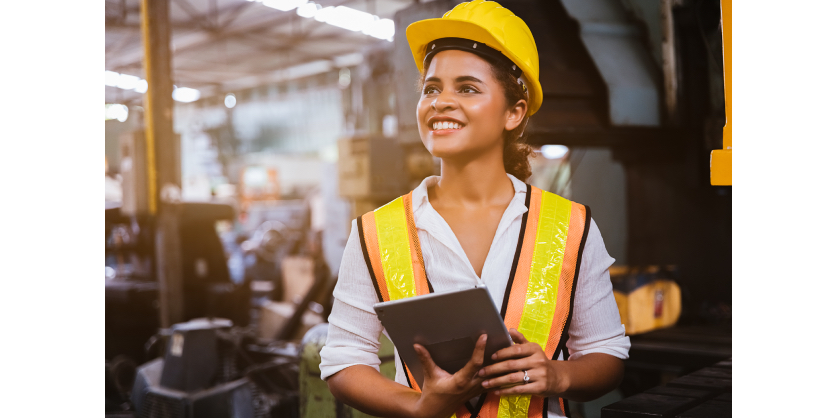
Nedco is an official Alliance Master Industrial Automation Distributor, which serves as a stamp of authentication to indicate to customers that they are the right partner. This recent achievement represents their high-level technical competence and expertise in the field of automation and digitalization.
“It means that we have training from Schneider Electric, it is technical training, and it is continuous. Every year we have more than 100 hours of training, we do tests, and we need to pass. For the customer, it means that we have knowledge, and we can help them. Unlike another distributor that just sells the parts, we offer support and can build an architecture because we know the product, the concept, and we can go deeper into the technical aspects of the project with the customers.”
Sébastien Larouche, Advisor in Automation and Motor Controls, Nedco Quebec
Rexel/Nedco is well positioned to help you upgrade your automation assets or plan and complete a migration properly. They are one of the largest distributors of electrical products in North America, they are supported with an ecosystem of leading manufacturers and systems integrators, and they have the qualifications to ensure that you succeed.
More Information
Related Story
Nedco is an Official Alliance Master Industrial Automation Distributor

Recently, the entire Nedco Automation team was excited to announce that they have officially achieved Alliance IAD Master certification as part of their partnership with Schneider Electric and their automation solutions. Read More