For Safety’s Sake: A Thorough Approach to Protecting Electrical Workers
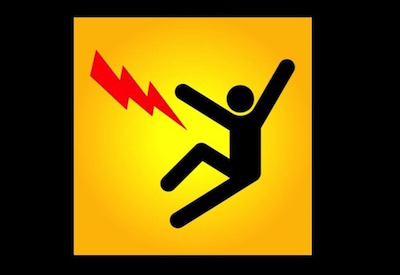
Nov 13, 2019
By Thomas Domitrovich
Electrical workers and facility owners rely on technical professionals to take prudent and economical steps towards increasing worker safety and protecting facility equipment. “Safety by design” describes, what I believe to be, a comprehensive approach to incorporating practical and feasible electrical distribution system design solutions.
The three pillars of success for electrical safety include:
1. eliminating hazards by establishing electrically safe working conditions
2. implementing designs that reduce the likelihood of a hazardous occurrence
3. reducing the potential severity of injuries should an accident occur when justified energized work is required
When our industry is focused on these three pillars, the result is safer conditions for electrical workers and better protected equipment.
Safety by design — A three-part approach
Every electrical product and system must be designed with worker and equipment safety in mind. The following section explores in more detail the safety by design approach and its three components.
Part 1: Eliminate the hazard
Hazard elimination is the act of establishing an electrically safe working condition. The NFPA 70E (National Fire Protection Association) committee helped provide clarity around this topic by adding an informational note to the definition of an electrically safe work condition, which reads as follows:
“An electrically safe work condition is not a procedure, it is a state wherein all hazardous electrical conductors or circuit parts to which a worker might be exposed are maintained in a de-energized state for the purpose of temporarily eliminating electrical hazards for the period of time for which the state is maintained.”
Establishing an electrically safe working condition is critical. While de-energizing equipment is an important goal, a worker will always have to dress in appropriate personal protection equipment (PPE) and use a test instrument to verify absence of voltage. Lock-out/tag-out procedures have to be followed which can range from simple to complex. In fact, there can be situations (e.g., verifying absence of voltage) when there isn’t PPE with a rating high enough to protect the worker. For those situations, I believe we must incorporate system designs and solutions that minimize the likelihood of an occurrence and the severity of injury should an accident occur.
Part 2: Designing for a reduction in the likelihood of occurrence
The following examples illustrate the many layers of safety that can be employed to reduce the likelihood of arc flash, arc blast and/or shock.
• Electrical one-line diagrams: an important part of a facility’s electrical infrastructure life begins even before ground is broken. This document is developed and used by engineers, suppliers, inspectors, workers and designers. Workers could be put at risk if one-line diagrams are not maintained and power system capabilities reviewed and updated as they change over time.
• Barriers: adding a local disconnect next to a panelboard or industrial control panel (ICP) that is accessed frequently for service provides electrical workers with clear visible indicators that the panel or ICP has been de-energized when the circuit breaker or switch is in the off position. When required absence of voltage testing is performed, the likelihood of an incident has been reduced.
• Disconnects: by placing a circuit breaker or fuse and switch in its own enclosure next to equipment, electrical workers have a readily accessible disconnect to remove voltage and establish an electrically safe working condition.
• Visibility: equipping a panelboard with a window that allows workers to visibly see the blades being disconnected aids in worker verification reducing the likelihood of an incident.
• Indicators: the presence of voltage indicators employed on equipment provides electrical workers a visible indication of which side of the disconnect is energized and which isn’t.
• Knowledge: information on the condition and maintenance of equipment can provide electrical workers details that are critical to safety when performing justified energized work. Knowledge of the equipment itself is critical to recognizing hazards.
• Working space: sometimes safety doesn’t come in the form of a product, it can simply be in the fact that a design provides adequate working space for the electrical worker to safely perform functions.
Part 3: Designing for a reduction in the severity of injuries
When justified energized work must occur, minimizing the danger associated with electrical hazards to the point at which injuries may be minor can be designed into the system. To that end, I see a variety of ways in which the electrical industry is making efforts to reduce the severity of injuries to workers should an accident occur.
• Decreased clearing time: by placing a circuit breaker with arc reduction maintenance switch technology or a fuse and switch in its own enclosure next to an upstream of electrical equipment likely to be a part of justified energized work provides reduced clearing times for arcing currents reducing the level of incident energy exposure. The achieved incident energy reduction downstream can be significant such that minimal PPE is required, which could also decrease the likelihood of an event occurring.
• GFCI shock protection: GFCIs are specifically designed to protect people against electric shock from an electrical system, and to monitor the imbalance of current between the ungrounded (hot) and grounded (neutral) conductor of a given circuit.
• IEEE 1584 and arc flash calculations: new updates to the 2018 Guide for Performing Arc Flash Calculations offer significant changes that impact the way arc flash hazards in electrical systems are analyzed. More precise calculations help reduce the risk to employees and contractors.
• Arc reduction technologies: arcing faults that occur within equipment need to be cleared as quickly as possible. Arc flash reduction technology reduces clearing times of arcing fault currents should a problem occur when working on energized electrical equipment. Arc quenching equipment can extinguish an arc flash in approximately 4 milliseconds. Eaton’s Arc Quenching Magnum DS low-voltage switchgear is a great example of such equipment: www.eaton.com/us/en-us/catalog/low-voltage-power-distribution-controls-systems/arc-quenching-magnum-ds-low-voltage-switchgear.html
A trio of documents critical to safety
All of us in the electrical industry look to three key documents from the National Fire Protection Association (NFPA) that strategically work together to help increase safety for electrical workers by providing guidance and recommendations:
• NFPA 70 The National Electrical Code (NEC) provides installation requirements
• NFPA 70E-2021 covers the topic of electrical safety in the workplace
• NFPA 70B covers electrical equipment maintenance
In particular, NFPA 70E includes requirements for safe work practices to protect personnel by reducing exposure to major electrical hazards, including shock, electrocution, arc flash and arc blast. These requirements rely on the fact that an electrical system was installed in accordance with the NEC and that maintenance has been performed leveraging reference materials found in NFPA 70B.
I’m pleased to report that recent changes to 70E highlight how important it is to design safety into systems and provide more detailed guidance for electrical workers. For example, the document addresses when the estimated incident energy exposure is greater than the arc rating of commercially available arc-rated PPE. We now have guidance for the purpose of absence of voltage testing. The following examples of risk reduction methods could be used to reduce the likelihood of occurrence of an arc flash, thus reducing the severity of exposure:
• use of non-contact proximity test instrument(s) or measurement of voltage on the secondary side of a low voltage transformer (VT) mounted in the equipment before use of a contact test instrument, to test for the absence of voltage below 1,000 volts
• if equipment design allows, observe visible gaps between the equipment conductors and circuit parts and the electrical source(s) of supply
• increase the working distance
• consider system design options to reduce the incident energy level
In addition, the latest version of 70E recognizes the newly updated IEEE 1584, a resource that the industry will continue to explore and apply to new power system analysis studies.
Protecting electrical workers means never settling
In my opinion, the effort to protect electrical workers and electrical equipment comes back to the three pillars of safety by design:
• eliminate the hazard
• reduce the likelihood of an occurrence
• reduce the severity of injuries
As I mentioned, our goal has to be establishing an electrically safe working condition. For situations where justified energized work is required, designs must emphasize reducing the chances of something harmful occurring and reducing the severity of injuries should an accident occur.
When it comes to shock hazards, while we can’t reduce the current flow we can provide ways to avoid inadvertent contact. This means choosing specialized equipment that provides more fingersafe solutions and options for barriers that help prevent the worker from coming in contact with energized parts. In some ways, I believe we can judge the work we’ve done based upon the complexity of PPE required for a task.
When designing electrical systems and the devices that go into those systems, a critical goal needs to be simplifying and safeguarding designs, so when systems need service or repair, electrical workers are safe in minimal PPE that consists of little more than their daily wear. Ultimately, electrical workers and our industry as a whole benefit most from a “never settle” approach to safety. Purchasing PPE at a higher Calorie capability than your solution demands doesn’t spell success. We need to ask ourselves if we can do better. We don’t have to settle for double digit calorie events anymore. We can do better. If we always strive for solutions that drive energy into the dirt, workers will eventually be safe in any situation.
Thomas Domitrovich is Eaton’s Vice President, Technical Sales. This article was first published online: https://www.eaton.com/us/en-us/company/news-insights/for-safetys-sake-blog/protecting-workers.html